Preventive maintenance is a method of proactive maintenance management that relies on doing things ahead of time, before it becomes a problem.
In this article we’ll cover:
- What is Preventive Maintenance?
- Importance of preventive maintenance
- What Preventive Maintenance variants are there?
- Risk-based maintenance
- Calender- based maintenance
- Usage-based maintenance
- Which preventive maintenance strategy is best for your business?
What is Preventive Maintenance?
Preventive maintenance is a discipline that helps stop problems at the source. It reverses the logic of the popular adage ‘Why fix something that isn’t broken?’ Instead, preventive maintenance encourages stepping in ahead of time, doing checks and small procedures to keep on top of your assets, before an issue arises. Those involved in quarry production plants will be well-acquainted with the necessity of preemptively greasing and lubricating equipment. For instance, bearings on a conveyor belt require regular lubrication checks to prevent overheating, jamming or eventual breakdowns.
To others, an example that typically resonates is keeping on top of servicing your car – oil, fluid, and gas checks and ensuring all parts are running as they should before becoming a greater problem.
Essentially, it’s a maintenance strategy to prevent a breakdown, accident, or injury.
Importance of Preventive Maintenance
Unplanned downtime in the construction materials industry is a big no-no. Most industries will have scheduled maintenance days but having a breakdown in between scheduled maintenance days is highly undesirable. A busy quarry can be low on stock, and a breakdown can affect availability as well as the whole value chain to the end customer.
A breakdown can also pose a health and safety risk, with faulty machinery causing an accident or grave injury.
Avoiding this scenario is crucial and why choosing an effective maintenance strategy is so important.
What Preventive Maintenance variants are there?
There’s a range of varying maintenance strategies – some overlap and some have marked differences. It could be useful for example, to understand the difference between preventive vs predictive maintenance.Regarding preventive maintenance variants, the examples below are the most common.
Risk-Based Maintenance (RBM)
This is the practice of prioritizing maintenance routines towards your most valuable assets. If key machinery or assets break down it could put a strain on resources, such as time and bottom line Helping to categorize your maintenance tasks, based on the risk that it poses towards entire production lines, if left ignored, is what risk-based maintenance is all about.
Examples of where risk-based maintenance is applied:
Typically, in a processing plant, the most expensive and more complex parts, such as crushers, will need specialists to come in and fix an issue. So, this type of equipment often has risk-based maintenance applied to it, as the cost of unexpected downtime and rushing out specialist personnel to resolve sudden issues will be high.
Calendar-Based Maintenance
This strategy involves scheduling maintenance, based on set date intervals. This is maintenance that will be carried out regardless of what the state of your asset is. Although a common method, it’s also a process that is resource-heavy, as it can involve superfluous checks or the other extreme, result in insufficient maintenance and equipment breaking between scheduled maintenance dates.
Examples of where it can be applied:
Heavy machinery and OEM equipment often have set dates and time intervals for checks. It fulfills a function as it still ensures a check happens with continuous intervals.
Usage-based maintenance
This falls under a broader preventive maintenance strategy but is a form of predictive maintenance. Instead of scheduling maintenance checks with fixed time intervals, the maintenance is triggered based on for example odometer values or hours or time spent. It uses real-time monitoring of data to give a comprehensive view of the state of your assets.
Examples of where it can be applied:
An example is looking at odometer values of the material that goes over a conveyor belt. After the conveyor belt has handled 10,000 tons, you will want to set a trigger to ensure a maintenance check is done.
Which type of preventive maintenance strategy is best for your business?
When evaluating usage-based, calendar-based, and risk-based maintenance strategies, the best preventive maintenance strategy for your business will depend on specific operational needs, asset criticality, and resource availability. It will often boil down to the size of your business including the range of assets you have.
Calendar-based maintenance might incur costs due to potentially unnecessary servicing of low-risk assets but tends to be the more common maintenance method preferred by small to medium-sized companies.
Usage-based maintenance usually involves high costs as it requires systems that incorporate comprehensive data, making it more appropriate for state-of-the-art sites, plants, and equipment.
Risk-based maintenance offers a midway solution regardless of company size, as it ensures your most valuable assets don’t come to a standstill.
With CheckProof regardless of the maintenance strategy you choose, the platform will accommodate your business. The customizable platform supports real-time integration for usage-based maintenance, scheduled reminders and checklists for calendar-based maintenance and tools for prioritizing tasks in risk-based maintenance, ensuring efficient execution and monitoring of all maintenance activities from one single platform.
Want to know what CheckProof can do for you?
CheckProof's easy-to-use app makes it easier to do the right thing at the right time. Discover how you can run world-class maintenance that is both cost-effective and sustainable.




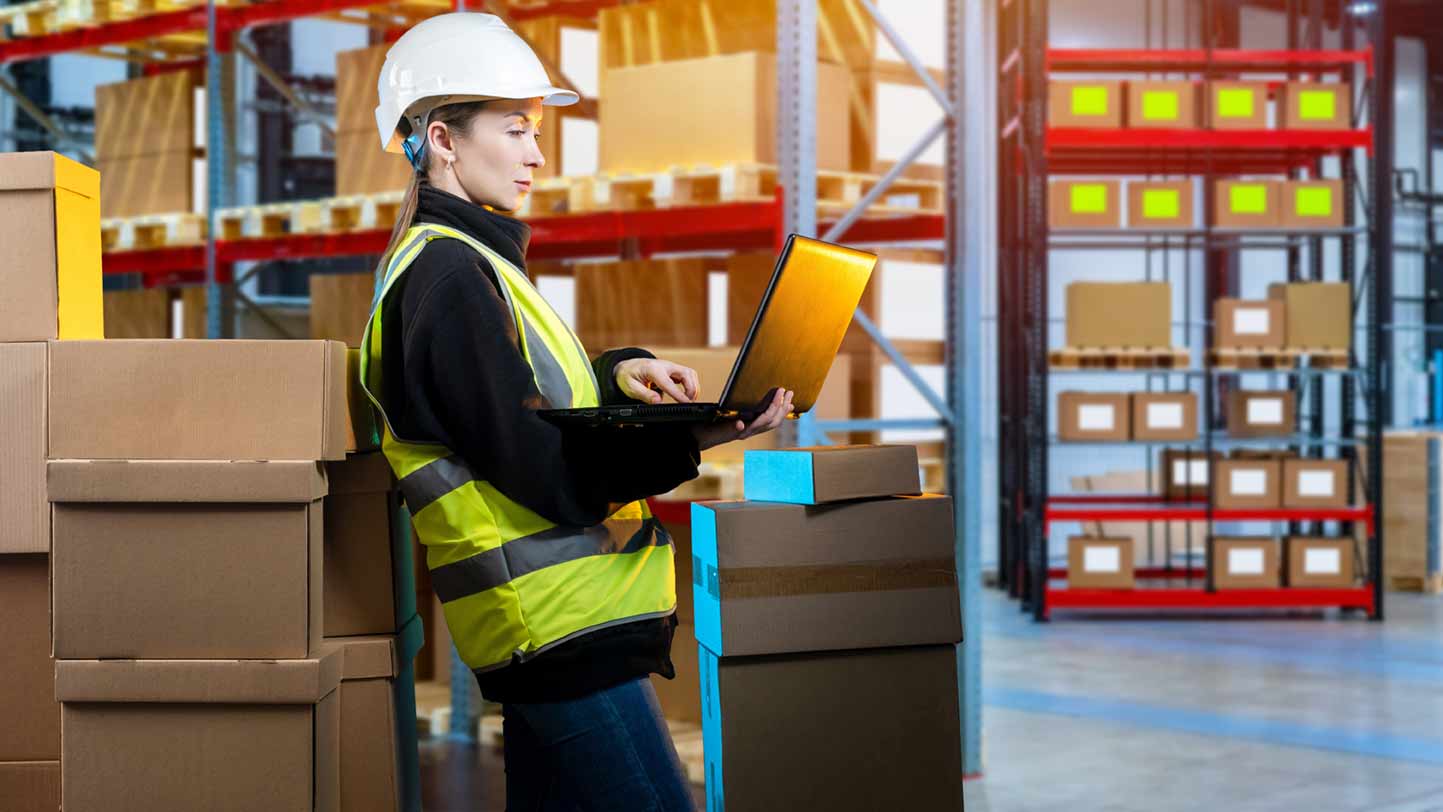

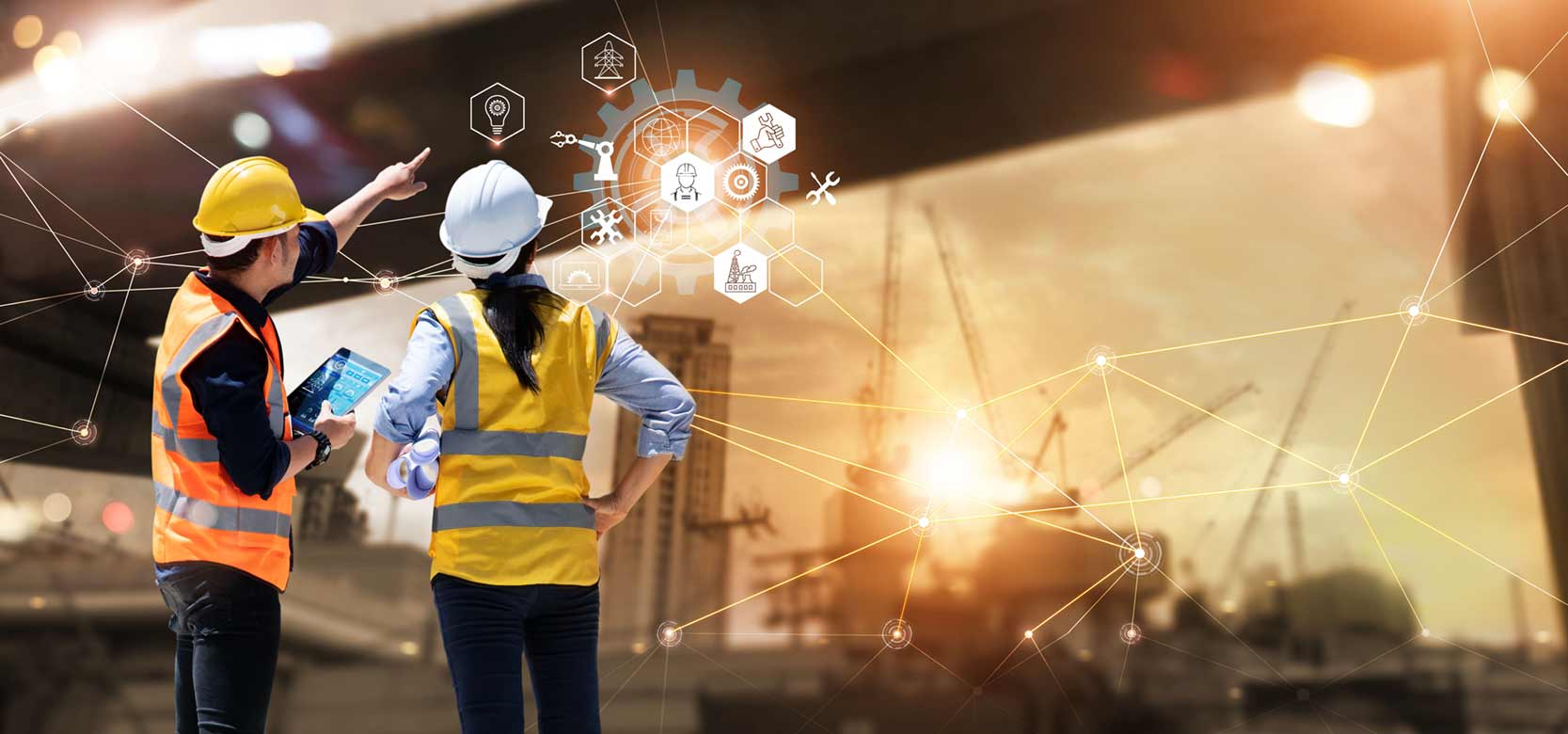


