Setting up SOPs (Standard Operating Procedures) for crucial tasks is an effective way to ensure safe and consistent work methods across your heavy industry sites. At least if your SOPs are available, relevant, and easy to use for frontline workers – which is, unfortunately, not always the case. This article offers you eight best practices that will help improve SOP compliance by adapting your instructions to suit the people who depend most on them.
What are SOPs, and why are they important?
An SOP, or Standard Operating Procedure, is a detailed step-by-step guide on how to perform a certain task in a safe and correct manner. The purpose of the SOP is to ensure a task is carried out the same way every time, regardless of who’s doing it.
How are SOPs used in heavy industries?
Heavy industry sites, like aggregate quarries or asphalt production plants, rely on complex equipment. Maintaining and servicing these machines might be relatively easy for a trained mechanic or fitter. But those aren’t always available on-site.
Well-put-together SOPs enable less experienced frontline operators to carry out basic maintenance tasks and solve minor issues directly instead of having to call a contractor and wait for them to come to the site. This minimizes unplanned (and costly) halts in production.
Joe Cage, Customer Success Manager at CheckProof, explains:
– A good SOP is like an IKEA manual for heavy industry equipment. It should be detailed and easy to follow. That way, an operator without previous experience with a particular crusher or screener can do routine maintenance and simpler repairs on it in a safe way. For more complex issues, for example, if welding is required, you’ll still need a specialist.
8 best practices to ensure SOP compliance across your frontline teams
Based on his extensive experience in creating SOPs for frontline teams, Joe shares the following dos and don’ts for successful implementation and long-term compliance:
1. Consider your user
Put yourself in the shoes of a frontline operator who’s new to the site and the equipment. What do they need to know to perform the task safely? For example, don’t just write ‘take the cover off’. You need to elaborate. Add detailed step-by-step instructions such as what the cover looks like, how to find it on the machine, how to take it off, where to put it once it’s off to avoid tripping over it, and so on.
2. Divide your SOP into manageable portions
Information is harder to take in when it’s served in big bulks, regardless of whether it’s in the form of printed papers or a seemingly endless document that you have to scroll through.
A digital SOP presented in a mobile-friendly interface lets you divide your instructions into manageable portions. The operator needs to confirm the completion of one step before moving on to the next, which helps them focus on one thing at a time.
3. Include visuals in your SOP
Adding pictures to your instructions will make them much easier to follow than if a task is described using text only. Video recordings of crucial steps will further reduce the risk of mistakes and misunderstandings.
4. Get frontline feedback on your SOP before fully implementing it
If frontline staff don’t understand or see the point of an SOP, they’re much less likely to follow it in their daily job. Therefore, once you’ve drafted a new SOP, let a staff member go through the different steps under your supervision. This way, you’ll get direct feedback and can adjust the instructions wherever necessary before implementing it at all relevant sites.
5. Leverage digital documentation – including time duration
One of the key benefits of digitizing your SOPs is that you automatically get a detailed record of all completed tasks, including date, time, and confirmation from the operator on-site. In case of an audit, you can always go back to ensure that staff members have accessed the right instructions.
A digital SOP also enables you to log the time frontline operators spend on each step of the prescribed process. This way, you can detect any deviations from the expected duration. For example, if a task that should take two hours has been completed in just a few seconds, you can assume it hasn’t been done properly and follow up.
6. Use a consistent format for all your SOPs
When you use the same template or layout for all your SOPs, your frontline staff will get familiar with the structure and how to navigate it. This lets them absorb the information quicker, even if they’re presented with a task for the first time.
7. Make sure your SOPs are available on mobile
Far too often, SOPs are only available on paper and kept in a binder in the site manager’s office. If they exist in digital format, they tend to be stored on servers or intranet pages requiring desktop computer access. And where there’s a lack of accessible documentation for frontline staff, there’s typically also a lack of routine compliance.
The solution to this challenge is ensuring your SOPs are available on mobile devices – ideally in an app that supports offline mode. This way, your frontline workers never need to look further than their own pocket to find an updated SOP for any task or machine around your plants or quarries.
8. Keep your SOPs up-to-date
SOPs need to be continuously reviewed and adjusted to stay compliant with updated HSEQ standards and policies at your company, as well as changes in government regulations. Schedule reminders at an appropriate time interval to ensure you revisit your SOPs regularly.
Digital tools let you update your SOPs across all relevant sites simultaneously, which is crucial from a workplace safety perspective. For example, an accident or incident at one site will require SOP updates across all similar sites to prevent the same thing from happening again somewhere else.
Your guide to HSE compliance
Want to find out how you can leverage digital technology, behavioral change, and maintenance best practices to improve workplace safety in your organization? Download our guide to ensure HSE compliance across your sites.
Want to know what CheckProof can do for you?
CheckProof's easy-to-use app makes it easier to do the right thing at the right time. Discover how you can run world-class maintenance that is both cost-effective and sustainable.

Revolutionizing Compliance: Banner Contracts on managing ISO audits with CheckProof

Implementation of Digital Systems: Rolling Out CheckProof Across Teams

From Fuel Savings to Production Gains: Cemex Germany’s Wins with CheckProof

A Recap of the CheckProof Industry Event & 10th Anniversary Celebration
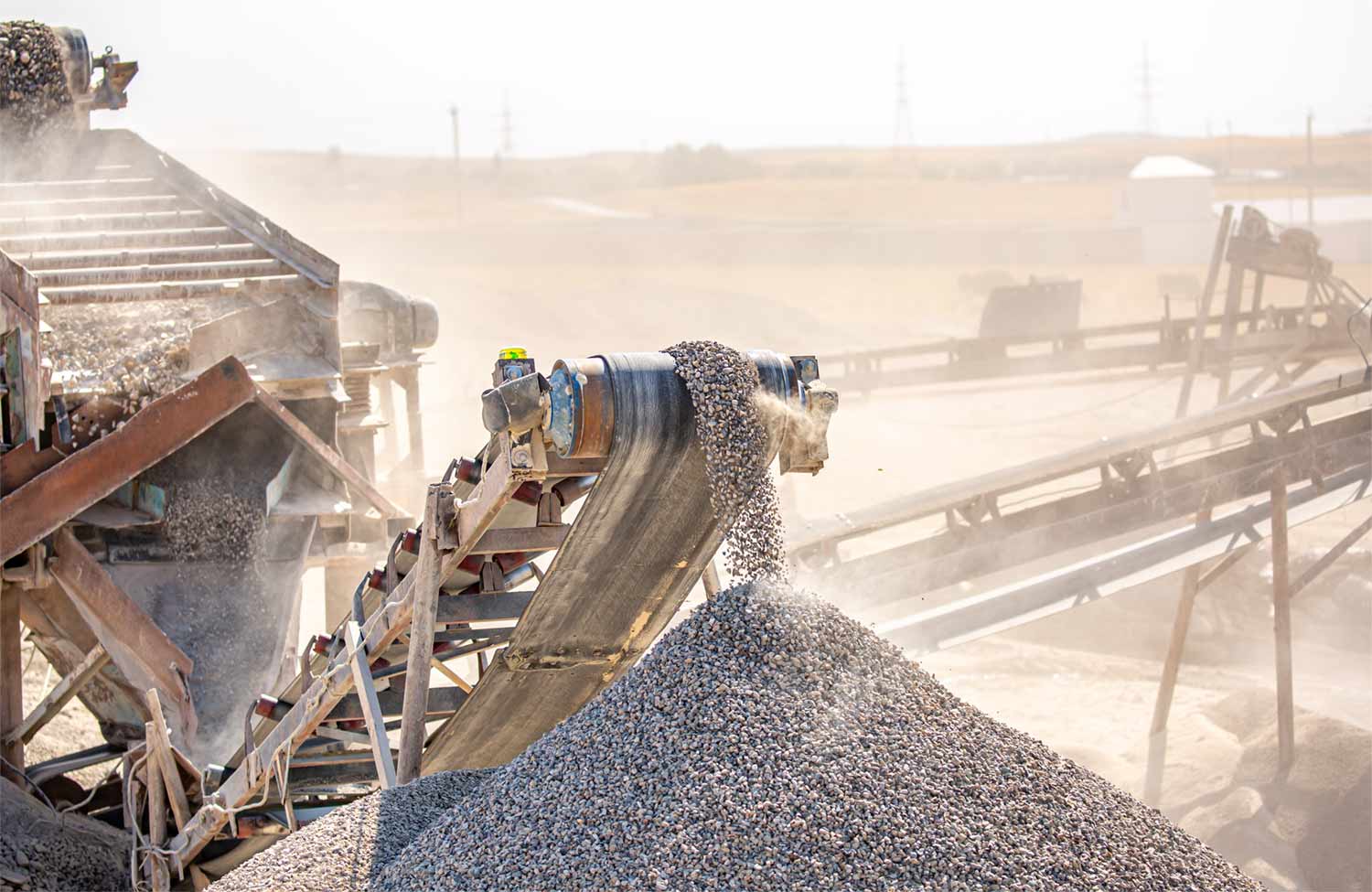
Trend Report: Key moments in the Construction Materials industry (2014–2024)

Meet Marcus Edlund, CheckProof’s First Employee and Tech Trailblazer

10 Key Technology Advancements in the Construction Materials Industries

SBMI’s Climate Roadmap for a Fossil-Free Aggregate Industry by 2045

HSEQ trends in the Construction Materials and Heavy Industry
