Without exaggeration, health and safety in the workplace is a matter of life and death. ILO (International Labour Organization) estimates the yearly number of work-related deaths globally to be nearly 2 million. Creating and maintaining a solid HSEQ framework is crucial for protecting your employees – but also your business – from harm. This comprehensive article will walk you through the key areas of HSEQ and what you need to set up a successful strategy.
Table of contents:
- HSEQ – what it means and why it’s important
- HSE, HSEQ, HSQE, EHS, and OHS – what’s the difference?
- What is an HSE Management System?
- 5 key elements of HSE management – and how to get them right
- International standards for HSE
- Industry-specific health and safety hazards
- The benefits of using a digital HSE management system
HSEQ – what it means and why it’s important
The first two letters of HSEQ stand for health and safety, which is about preventing workplace accidents and injuries in the short term, as well as promoting the overall health and well-being of your employees long-term.
The E for environment refers to actions aimed at reducing your company’s negative impact on the environment – from local factors like waste management to the entire carbon footprint.
Q for Quality is about having processes in place to monitor and control the quality of what you’re producing. The aim is to maintain a consistently high level in your delivery to your customers – without compromising on the health, safety, and environmental aspects.
For all of these areas, there are legal requirements and industry standards that your company needs to comply with both on a local and international level. Of course, a well-structured HSEQ framework will support your internal operations and make your business safer and more effective. But it will also help you present valid documentation of your routines and processes to relevant authorities, for example, during health and safety, environment, or quality audits.
To succeed with your HSEQ strategy, you need to focus on both the technical and human aspects. Ideally, these two elements support each other. For example, a digital system for effective documentation, reporting, and following up will make routines more accessible and motivating to staff. It also helps your managers detect any negligence when it comes to following correct procedures, as well as share positive examples to inspire others.
HSE, HSEQ, HSQE, EHS, and OHS – what’s the difference?
The business world is full of abbreviations, and HSEQ is no exception. Below you’ll find the most commonly used acronyms. As you can see, the individual words have the same meaning but appear in different combinations. Which acronym to use will depend on how your organization is built around the different areas and which parts you want to emphasize. For example, whether you should treat Quality Management as a separate entity or not. There are also some variations in terminology between industries and regions.
HSE: Health, safety, and environment
HSEQ: Health, safety, environment, and quality
HSQE: Health, safety, quality, and environment
EHS: Environment, health, and safety
OHS: Occupational health and safety
OSH: Occupational safety and health
What is an HSE Management System?
An HSE management system is the framework that an organization uses to maintain a safe workplace, and where routines and procedures comply with relevant health, safety, and environmental legislation. But what does this mean in practice? The exact structure varies between organizations, but there are certain key elements you need to have in place.
5 key elements of HSE management – and how to get them right
1. Policy
Your HSE policy is the foundation on which your practical health and safety routines rest. This is where you state the intent and commitment of your company, as well as which role or person is responsible for which part. To be effective, your policy needs to be clear, straightforward, and easily accessible. If it’s collecting dust on a shelf, your frontline staff aren’t likely to know about it, let alone follow it.
Your policy should also include practical actions. E.g. doing risk assessments, training staff, putting up signs, and making sure staff use certain safety equipment. Review your policy regularly to ensure it’s always up to date and compliant with relevant legislation.
2. Planning
How will your organization achieve the goals stated in your policy and make sure the required actions are carried out? You need a plan and a clear management structure to succeed. All managers and employees should have relevant health and safety objectives that can be measured and followed up continuously.
3. Implementation
To successfully implement your HSE plan, you need to make it a natural and integrated part of the day-to-day across your organization. Establish a safety culture by involving frontline staff in assessing risks and determining how these can be eliminated or minimized. Empower and motivate employees to work in a safe and compliant way. It’s also vital that senior managers actively promote and encourage HSE compliance. This will reduce the risk of staff cutting corners because they think hitting production targets is more important than following safety routines.
4. Measuring performance
To maintain a high level of HSE compliance over time, you need to measure, monitor, and evaluate your organization’s performance. Use a combination of active and reactive assessment measures.
Active assessments can include:
- regular inspections and audits in the workplace to determine how well employees are following routines
- collecting feedback from staff training sessions on health and safety
- continuously reviewing local risk assessments with local teams
Reactive assessments can include:
- investigating underlying causes when staff fails to comply with routines, and set up additional training where necessary
- analyzing records of accidents, injuries, and near misses to identify the causes and take measures to prevent them from happening again
5. Auditing and reviewing
Is your organization reaching the goals stated in your policy? If not – what changes do you need to make to your HSE management system to improve the results? Use data from both internal monitoring and independent audits to benchmark performance against your company’s KPIs, as well as against industry best practices and the performance of your competitors. Proactivity is key: don’t wait until an inspection from an external auditor before you take action. Instead, include the auditing and reviewing of your company’s HSE performance in your overall efforts for continuous improvement.
—
Want to learn more about how to make HSE an integral part of your operations? Don’t miss our guide How to ensure complete HSE compliance across your sites.

To ensure complete HSE compliance across your sites, you need to make HSE an integrated part of your daily operations – and assure that everyone knows the consequences of not following the rules. This guide is packed with best practices on how to enable behavioral change and ultimately keep your employees safe.
International standards for HSE
Standards are effective tools that help make sure you’re following best practices and established expertise. The International Organization for Standardization (ISO) has published thousands of standards that are used worldwide in different areas of business and technology.
What are the most important ISO standards within HSEQ?
ISO 45001 is a standard within the ISO 45000 family of occupational health and safety standards. ISO 45001 (which replaced the OHSAS 18001 standard in 2018) describes requirements for an occupational health and safety (OH&S) management system. It also guides organizations on using such a system to successfully prevent injuries and ill-health in the workplace. 45001:2018 is the latest version of this standard (as of 2022).
ISO 14000 is a family of standards focusing on helping organizations reduce the negative environmental impact of their operations. One of the standards included is ISO 14001, which describes how organizations can design and implement an effective environmental management system (EMS). The current version of ISO 14001 is ISO 14001:2015.
ISO 9000 is a series of standards for effective quality management. They are based on the seven quality management principles (QMP):
- Customer focus
- Leadership
- Engagement of people
- Process approach
- Improvement
- Evidence-based decision-making
- Relationship management
Included in the series is the ISO 9001 standard that sets out the criteria for a quality management system (QMS). The purpose of ISO 9001 is to help companies ensure that they can provide their customers with consistent, good-quality products and services.
Industry-specific health and safety hazards
The importance of HSE in heavy industries can not be underestimated. Sectors such as mining, aggregates, oil and gas, construction, and the energy sector have several risk factors in common. OSHA (the US Occupational Safety and Health Administration) has summarized the deadliest occupational health hazards as the Fatal Fours:
- Falls
- Struck-by
- Electrocution
- Caught in-between
Safety risks in the construction sector
Construction is the deadliest industry for workers. In the US, 21% of fatal work injuries occur in this sector. The ten most common causes of death on construction sites worldwide are:
- Falls
- Electrocution
- Crushing injuries
- Caught-between injuries
- Crane collapse
- Fires
- Asbestos, ionizing radiation, and cancer-causing chemicals
- Slips and trips
- Exhaustion
- Heat strokes
Safety risks in the energy sector
According to OSHA, 60% of fatal on-site accidents in the oil and gas extraction industry are caused by struck-by/caught-in/caught-between hazards. These often involve moving vehicles or equipment, falling equipment, or high-pressure lines. Other common risk factors in the oil and gas industry are:
- Vehicle collisions
- Explosions and fires
- Falls
- Confined spaces
- High-pressure lines and equipment
- Electrical and other hazardous energy
- Machine hazards
HSE and the energy transition
How is the transition from fossil fuels to renewable energy sources affecting employee safety? As this article from Our World in Data shows, energy sources that are cleaner from an environmental perspective are also generally safer for the people involved in the production. A positive side effect of shifting from fossil fuels to renewable energy sources, such as wind and solar power, could be a significant decrease in work-related deaths in the energy sector.
That said, many common health hazards – such as falling – also occur in the green energy sector. Others might even become more common. For example, workers in the wind energy sector can face a risk of asphyxiation due to low oxygen levels in confined spaces. In the solar energy industry, workers risk exposure to hazards such as arc flashes, electric shock, and thermal burn.
The benefits of using a digital HSE management system
To prevent severe accidents in the workplace – and comply with relevant regulations – you need well-documented policies, routines, and processes for all aspects of your HSEQ work. But having routines is one thing. Having staff follow them is another. If you keep your HSEQ documentation in a binder sitting on the shelf of the site manager’s office, your frontline staff is not very likely to integrate correct safety routines into their day-to-day tasks. Luckily, the digital evolution of recent years has brought whole new possibilities.
With today’s digital HSE management systems, you can make your documents and routines interactive and easily accessible to staff at all levels. Digitization also makes customizing and updating your policies much more streamlined.
To successfully implement a digital HSE management system, make sure you choose a platform that is:
- user-friendly
- mobile-optimized
- customizable
Do you want to digitize your HSE management? Get inspired by how Preem – Sweden’s largest fuel company – implement a new digital in-plant inspection tool at record speed.
5 ways CheckProof supports your HSE strategy
Heavy industry businesses worldwide use CheckProof’s mobile-first platform as their primary tool for maintenance routines, quality control, and HSE management. Below, you can see examples of features in the platform and how they can support your HSE efforts.
1. Customized checklists for all your HSE routines
Set up customized and easy-to-follow checklists, including pictures, in CheckProof. This way, each employee will know exactly what to look for, and can tick off their tasks directly from their mobile devices as they complete them. HSE checklists could include:
- Safety rounds & observations
- Job safety analysis (JSA)
- Self-checks PPE
- Fire protection controls
- Supervisory rounds
- Internal audits
- Fluid consumption reporting
- Risk assessment
2. RFID tags for added security
When it comes to health and safety, there’s no room for uncertainty. With CheckProof’s RFID feature, you can attach RFID tags to critical control points at your sites and connect these tags to corresponding checklists in the platform. To mark the check as complete, the employee responsible has to scan the tag on-site in their CheckProof app.
3. Effective incident reporting & deviation management
CheckProof lets your frontline employees report incidents and deviations straight from the field into the platform, giving on-site managers a full overview dashboard where they can prioritize issues and make sure they’re seen to in time.
4. Full documentation at your fingertips
Since every task performed in CheckProof is logged, you always have full documentation for both internal stakeholders and external auditors. This also helps foster a culture of transparency and accountability.
5. Data-driven insights for continuous improvement
You can easily integrate CheckProof’s platform with other systems, including assets connected through IoT. This enables you to collect telematics data, as well as reports from frontline staff, and generate custom reports in your business intelligence tool. This will in turn help you detect patterns over time. Monitor everything from the frequency of safety incidents to excessive idle time and use these insights to optimize your operations and focus on the right continuous improvement initiatives.
Find out how CheckProof can help you make HSEQ an integrated part of the daily operations at your sites – book your demo today!
Want to know what CheckProof can do for you?
CheckProof's easy-to-use app makes it easier to do the right thing at the right time. Discover how you can run world-class maintenance that is both cost-effective and sustainable.




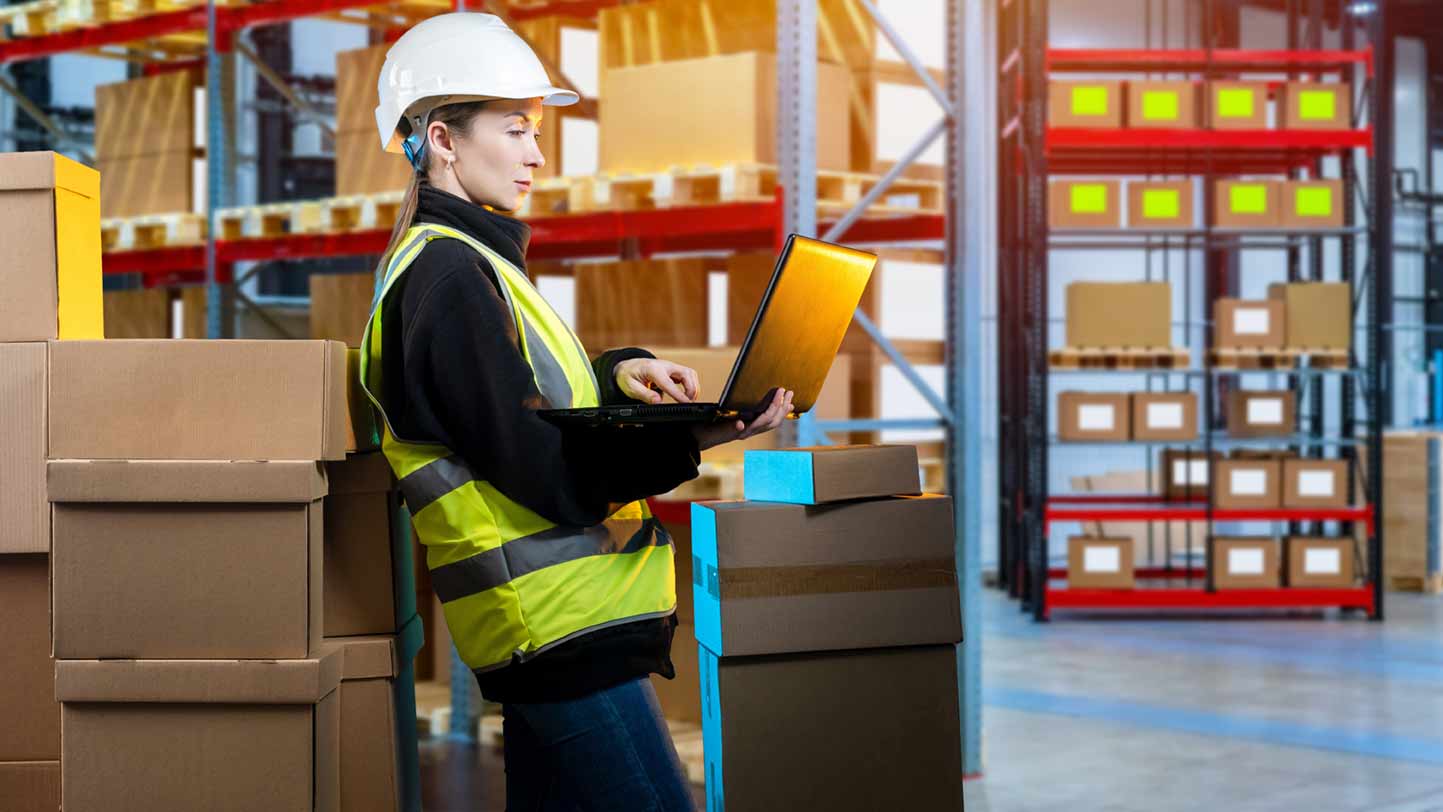

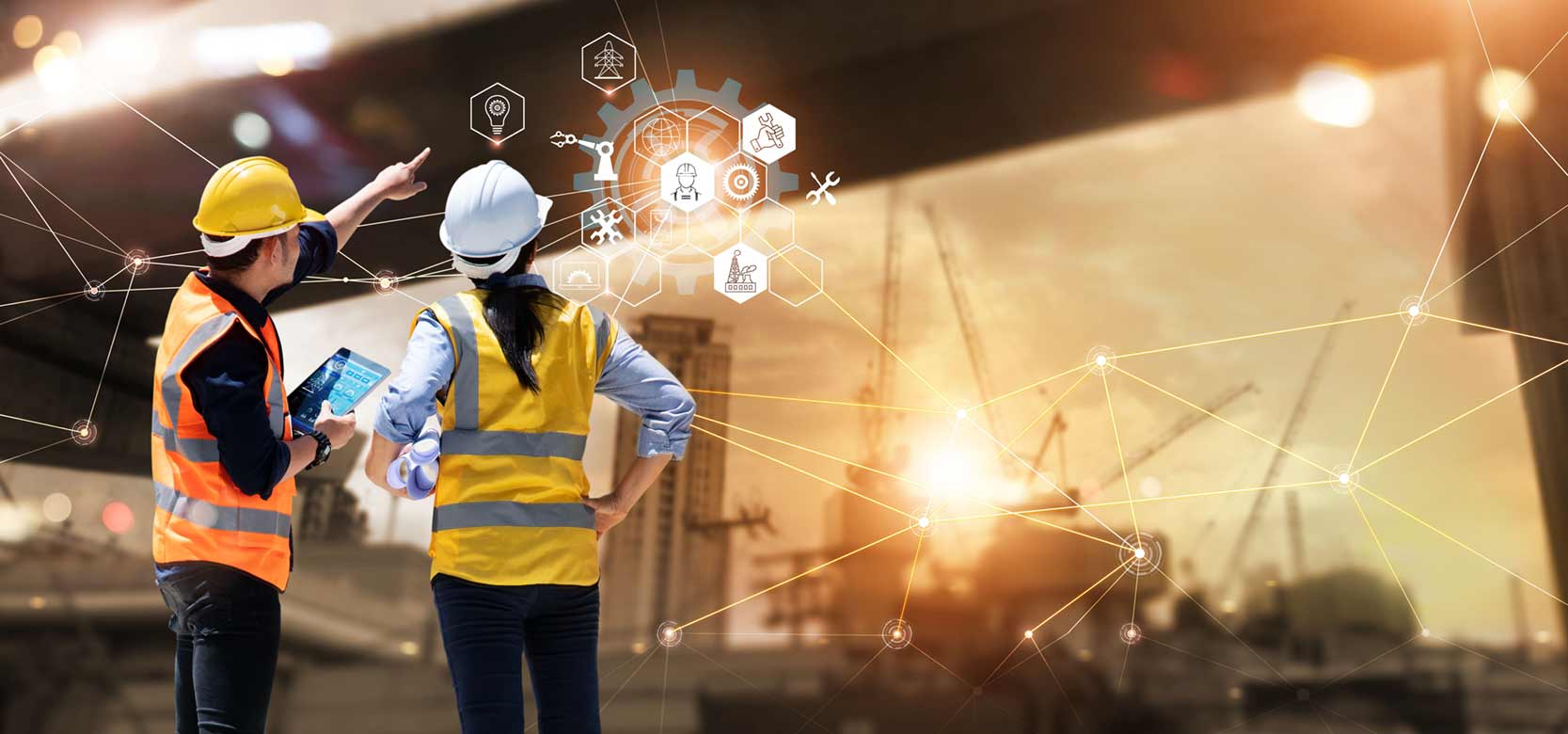


