Join us at AGG1, St Louis, MO - America's Center Convention Complex: 25-27 March
In the Construction Materials industry, setting up workflow processes for Health, Safety, Environment, and Quality (HSEQ) that are effective and easily adopted, is business critical. Ensuring smooth operations while keeping to stringent safety standards is non-negotiable.
However, many larger organizations that could benefit from one consistent and complete overview of their fleets and plants, often juggle multiple platforms and tools for maintenance and HSEQ management. Not only is this cumbersome and inefficient but can compromise their work and efforts on all HSEQ-related matters.
In this article we’ll cover:
- 9 Most common HSEQ challenges in the Construction Materials industry
- The drawback of using multiple task-management platforms across an organization
- 5 gains of combining Maintenance & HSEQ workflows
- 4 practical tips for improving on-site safety
- Checklists of 10 questions to ask when considering a HSEQ platform.
10 Most common HSEQ challenges in the Construction Materials Industry
Every organization and industry has its own set of unique HSEQ-related challenges. For example, Health & Safety Executive list the most common injuries in the quarry industry include manual handling, falls from heights, transportation, explosives amongst others.
We can all agree that advancing crucial HSEQ procedures across multiple sites and separate teams is therefore crucial and will inevitably save lives. Yet Health & Safety managers and site managers still mention some common challenges they struggle with, within the construction materials industry. We list the 10 most common challenges HSEQ professionals face below:
- Teams operating in silos – teams within the construction materials industry can often work physically far from each other. If they don’t have the means to communicate simply and instantly with other team members, information will fall between the cracks and for a Health and Safety or Quality manager, this lack of communication also translates into impaired visibility into their work and incident reporting.
- Routines aren’t followed – Standard Operating Procedures (SOPs) that seemingly work on paper, don’t work on the ground, and routines are skipped or postponed.
- Inefficient reporting tools for incidents, near-misses, and recurring deviations – a system that’s not customizable for the business’s needs will very likely become redundant and not something operators or frontline staff will use easily, leading to gaps in data and the same incidents repeating.
- Staff training & engagement: Ensuring comprehensive staff training and fostering a commitment to safety and quality measures are fundamental pillars of a robust HSEQ framework. Lack of training and time can contribute to shortcuts being taken, but also staff engagement can be low if they worry about getting into trouble when an accident occurs.
- Inadequate hazard/risk assessment analysis – this is crucial for identifying potential dangers and implementing effective preventive measures, but often a lack of insight and complete overview can compromise a hazard assessment.
- Compliance & regulatory requirements: Staying updated is essential to maintaining a safe working environment and avoiding legal repercussions. Yet keeping on top of new regulations and storing new (and old) policies in one place can pose a problem if all teams aren’t working from the same system.
- Quality issues not being actioned as well as the material not being correctly tested for quality – This could result in the customer receiving a faulty final product.
- Environmental logs which are needed for operation permits, is missed as well as environmental incidents such as contaminations and leakages aren’t logged or investigated appropriately.
- HSE emergency drills aren’t performed routinely.
- Records being misplaced and paperwork stuck on sites.
The drawback of using multiple platforms across an organization
Typically, many organizations use separate systems for maintenance and HSEQ management. While these platforms may serve the individual purposes adequately, managing them separately presents several challenges, and contributes to the challenges mentioned above that HSEQ managers face. Drawbacks of using multiple platforms typically include:
- Data Overview: With separate platforms, data is often ‘hidden’ across different systems, making it not only difficult to obtain a comprehensive overview of operations, but also to drill down to the root cause of certain issues, allowing recurring deviations to go unchecked.
- Workflow Agility: Switching between multiple platforms disrupts workflow continuity and increases the likelihood of errors or oversights. It also prevents workflow agility, as immediate action is often hard to take if platforms (read teams) aren’t speaking to each other.
- Multiple Software Integration: Integration issues between separate software systems hinder data exchange and synchronization, leading to inefficiencies and inconsistencies.
- Gaps in Staff Knowledge: Knowledgeable and competent staff is our most valuable asset – yet harnessing their skills and transferring their experience across teams, becomes almost impossible when operating in silos on separate systems.
5 gains of combining Maintenance & HSEQ workflows
As we’ve learned, there are several drawbacks of using multiple systems, but what are the immediate gains of switching to one platform, such as CheckProof?
We list 5 immediate gains of making that switch!
- One user-friendly dashboard and app for everyone: With CheckProof, users gain access to a unified dashboard that provides a comprehensive view of maintenance activities, incident-, near-miss reports, audits, quality issues and compliance status—all in one place. This eliminates the need to switch between multiple systems, saving time and reducing the likelihood of errors.
- Actions across teams can be triggered from one system: By centralizing maintenance and HSEQ processes, CheckProof allows seamless collaboration and communication among team members. If an incident is reported from one site, an action plan can be triggered across other sites. Such as creating actions that can be managed efficiently within the platform.
- Real-time Insights: CheckProof gives real-time insights into operational performance and tasks that affect compliance. Customizable checklists and reports enable informed decision-making with continuous improvement initiatives. Digital checklists that also can trigger tasks (through features such as push notices) mean that you can action issues instantly, without delay.
- API Integration: CheckProof seamlessly integrates with existing systems. For example, manage telematics data from machines and vehicles (from different brands) from the same platform. Combine the data with deviations reported by frontline staff to follow up on issues and ensuring routines are followed.
- Cost Saving: Maintaining multiple platforms incurs additional costs in terms of licensing, training, and support – choosing one platform will save costs. Try CheckProof’s calculators to see how you can decrease costs for your business.
4 practical tips for improving HSEQ on-site
Ultimately, we are all working towards the same goal, keeping our fleets, plants, and staff safe and accident-free and securing consistent quality. Keeping this in mind, it is worth checking in on the HSEQ targets that you have set for your site. Applying the 4 standards below for all your HSEQ-related work can help!
- Aim for increased Incident & Case reporting
- A user-friendly app makes reporting easy
- Simple access to updated forms
- Provide frontline staff with step-by-step guides
- Easy logging of Quality & Environmental incidents
- Collect all your Health & Safety Routines in one place
- Schedule safety checks with features like push notifications
- Mandatory Control Points
- RFID tags so you know tasks have been completed
- Ensure HSE Emergency drills are performed routinely
- Full Overview of Recurring deviations
- An admin panel enabling categorization, filtering and search
- Full overview of HSEQ issues
- Track safety observations and other data years back
- Improving quality control points with data
- Improving Traceability to meet Compliance
- Increase traceability and follow-up of inspections
- Easy documentation to facilitate compliance
- A platform that simplifies regulatory upkeep
CHECKLIST OF 10 QUESTIONS TO ASK WHEN CONSIDERING A HSEQ PLATFORM
If you’re considering an HSEQ work-management tool, ensure the platform you consider meets the criteria below.
- Customized digital checklists that can trigger tasks and action plans
- Fast log of incidents, near-misses, and deviations.
- Ability to create NCR-related actions from the platform to eliminate recurring incidents
- Only using one piece of software to manage different tasks (including maintenance and HSEQ)
- A digital platform that is designed uniquely for your industry.
- One platform should address different department needs.
- It should support API Integration
- Ability to log photos and record videos within the tool.
- A simple admin view coupled with a user-friendly frontline reporting app
- Ability to report deviations combined with telematics data from fleets.
Many organizations have departments operating in silos, yet each separate unit can have a knock-on effect on so many other functions. As an HSEQ manager, moving to one, single platform to solve for HSEQ and maintenance can lead to a string of unexpected benefits. Furthermore, applying technology that is uniquely designed for the construction materials industry can have a tremendous impact on the whole company, helping keep your personnel safe and your operations compliant.
It can be the game-changer you didn’t know you needed.
Want to know what CheckProof can do for you?
CheckProof's easy-to-use app makes it easier to do the right thing at the right time. Discover how you can run world-class maintenance that is both cost-effective and sustainable.

Maximize Efficiency with an OEE Monitoring System
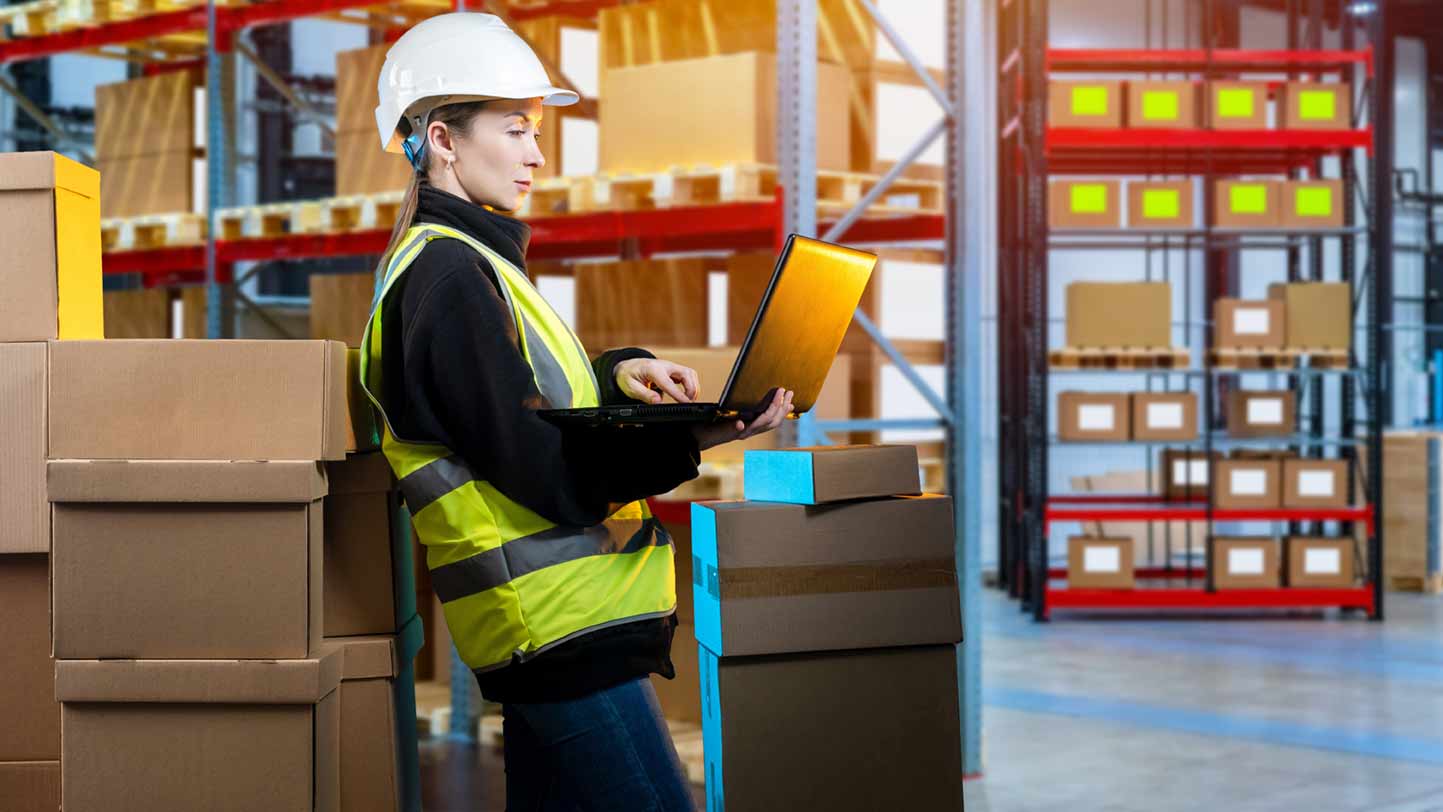
Plant Asset Management Software:Maximizing Equipment Uptime

Machine Downtime Tracking: The key to smarter, more efficient operations
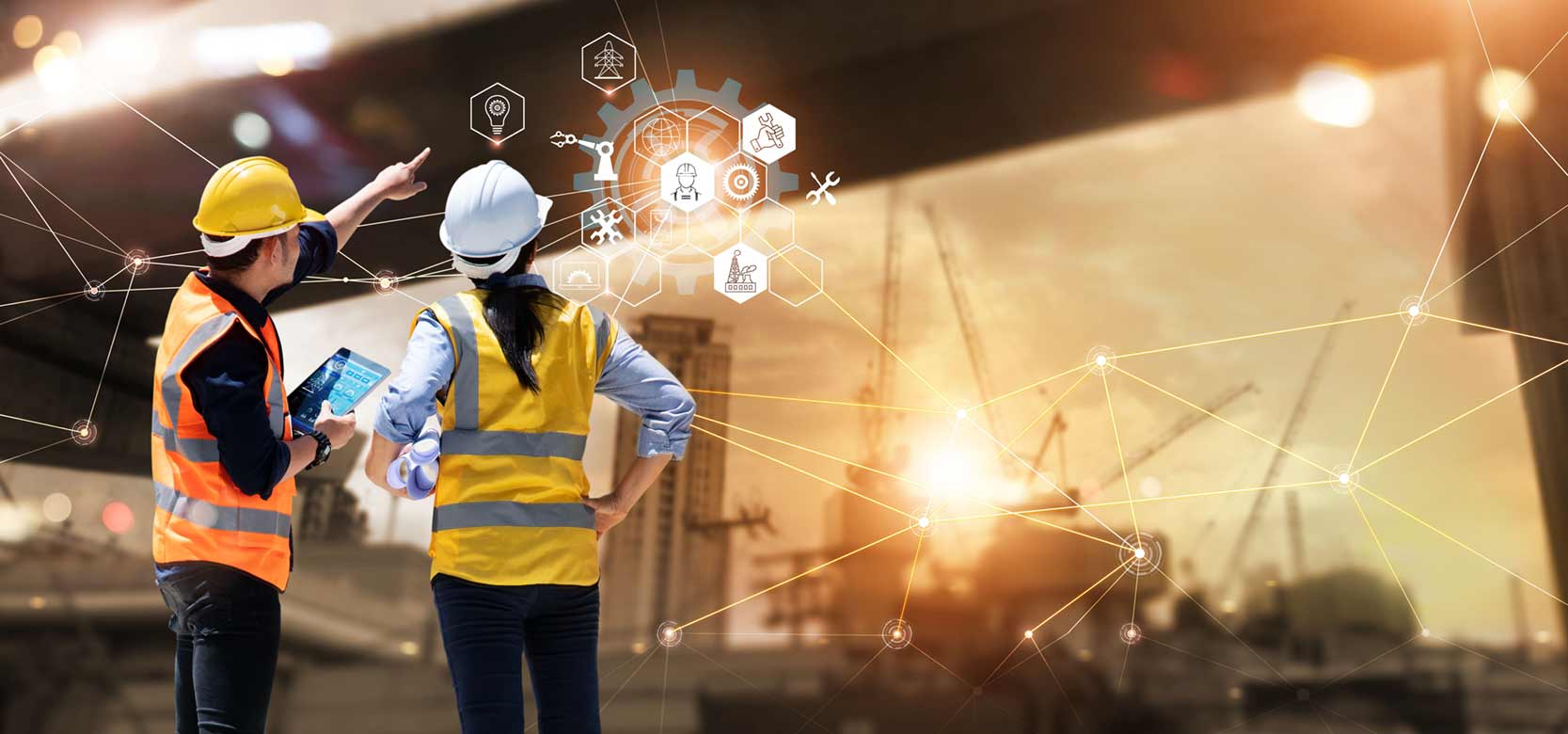
CMMS Software: What it is and why it’s key to First-Class Maintenance Operations

Revolutionizing Compliance: Banner Contracts on managing ISO audits with CheckProof

Implementation of Digital Systems: Rolling Out CheckProof Across Teams

From Fuel Savings to Production Gains: Cemex Germany’s Wins with CheckProof

A Recap of the CheckProof Industry Event & 10th Anniversary Celebration
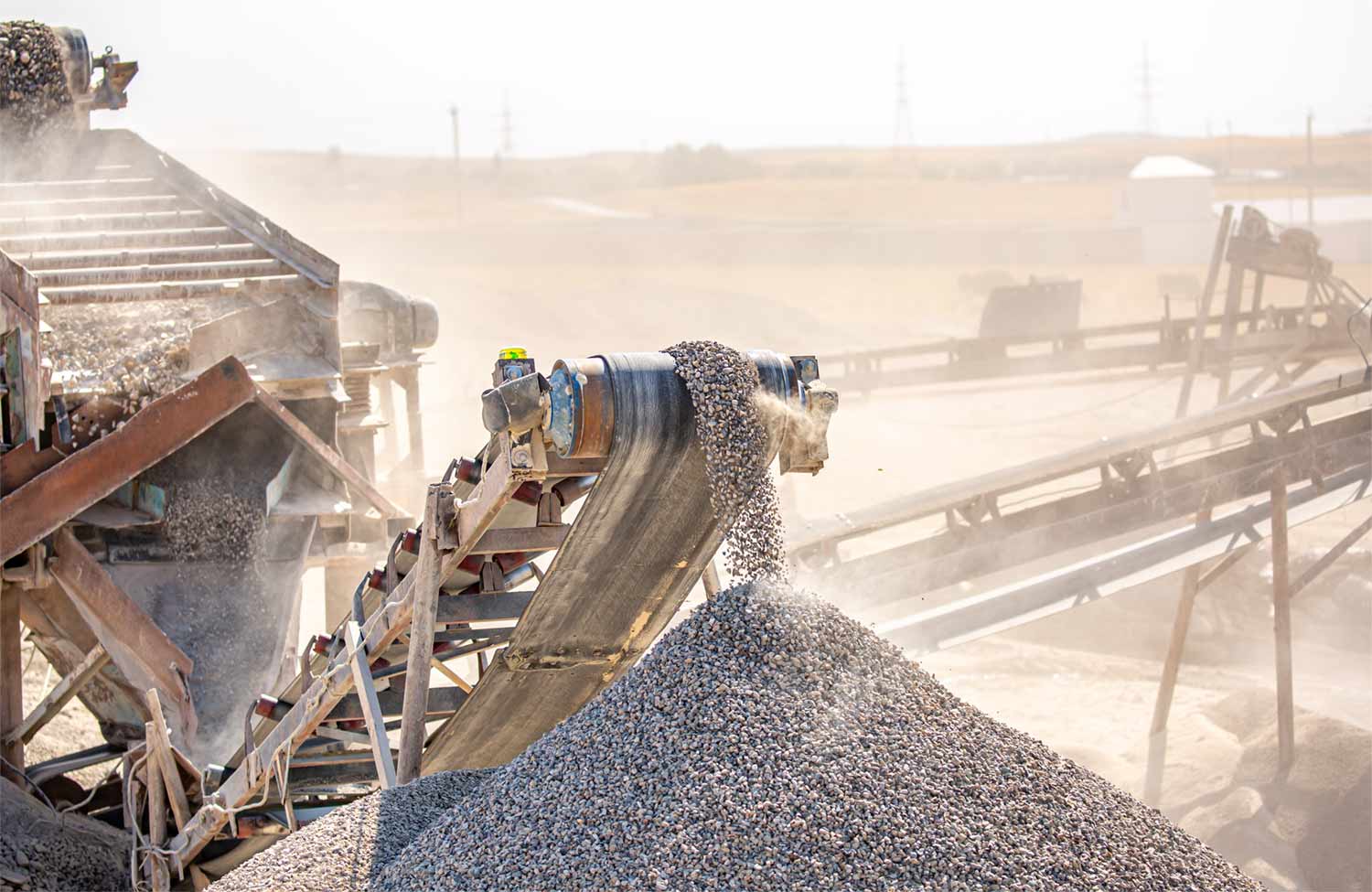
Trend Report: Key moments in the Construction Materials industry (2014–2024)
