The proverb ‘if you fail to prepare, then prepare to fail’, rings especially true when it comes to to the process of Pre-Task Risk Assessment (PTRA).
Failure to examine your work environment or equipment before performing a potentially hazardous task can leave you exposed to several things going wrong.
In certain industries, the outcome of a missed risk analysis, before undertaking any major work could be grave. Mitigating potential hazards with the help of a PTRA before work begins is your best bet for a successful and safe outcome.
In this article, we’ll walk you through:
- What is Pre-task risk assessment and why is it important
- PTRA, PTP, JHA and Take 5 – What’s the difference?
- 10 Fundamentals of a Pre-task Risk Assessment routine
- The 3 common mistakes of a PTRA and how to avoid them
- CheckProof’s approach to enhanced safety with PTRA templates and HSE compliance
What is Pre-Task Risk Assessment?
Pre-task risk assessment, as the name suggests, is the process of assessing or scanning the workplace and/or work equipment before undertaking a job or a task, with the intention of avoiding hazards AND ensuring the safety and wellbeing of staff. Unfortunately, even with the best of intentions, many organizations fail to implement this safety-mechanism routine into their workflow – leaving them exposed.
Why is Pre-Task Risk Assessment important?
Whilst the principal reason to perform a PTRA is to promote a safe work environment, a well-executed PTRA can also help you reduce cost and machine downtime. Spotting defects before beginning a job can save valuable time, allowing you to correct errors before beginning a task. Furthermore, it is a key step in keeping your sites HSE compliant whilst keeping a clear chain of accountability across the organization.
PTRA, PTP, JHA and Take 5 – What’s the difference?
When it comes to on-site risk preparation there are many different methods and routines that may at first glance seem conflated, but each serves a distinct purpose and contribute to mitigating risk and enhancing operational efficiency. Understanding what distinguishes each method, can help you decide which (or if all) of them are applicable to your industry and business.
- Pre-Task Risk Assessment (PTRA) – as mentioned above, this focuses on proactively identifying potential risks and hazards associated with specific tasks, before they are executed and implement controls to minimize the probability of an accident.
- Pre-Task Planning (PTP) is a broader process to include a detailed co-ordination of all aspects of a job. This can include, scheduling plans, resource allocation, equipment needs and stakeholder/task ownership mapping. This method whilst including safety aspects, is an overarching tool to help project planning and adhere to project timelines.
- Job Hazard Analysis (JHA) is a structured approach used to identify, assess, and control hazards associated with specific job tasks or work processes. Unlike PTRA and PTP, which are more focused on pre-task preparation and planning, JHA delves deeper into the operational and safety aspects and of individual job roles or activities as well as ensuring compliance with regulatory requirements.
- Take 5 is the grandfather of risk-safety assessments at work. One of the original safety routines established and one of the methods still most widely used. It typically is a reminder to: stop, look, assess, control, monitor. However, without clearer guidelines, this can be open for interpretation. Take 5’s should be done at the location of the work for best analysis. Sometimes these are done in the office but you then risk missing key issues.
10 Fundamentals of a Pre-Task Risk Assessment routine
So, what should you consider when mapping a PTRA routine or template? Although there will be requirements that are unique to your organisation, the list below are cornerstones of a solid PTRA template.
- Digital traceability: For starters, ensure your template is created digitally. Forego pen and paper and create a digital checklist that follows the entire assessment process to ensure you check off for each part of the PTRA. This will result in you not missing any crucial steps.
- Standardize templates: Develop a consistent and recognizable template to ensure thoroughness and reliability in PTRP assessments across varying tasks and environments. Not sure where to start? Checkproof offers customizable templates that can be used for PTRA assessments.
- Ease of use. Don’t underestimate this! If the PTRA template is overly complicated to follow or makes it difficult to complete tasks – chances are crucial steps will be overlooked. For example, with CheckProof you can easily drag and drop as you’re building checklists or changing them, and your frontline staff can communicate any defects seamlessly without jumping through hoops.
- Clear accountability: Each step completed and especially before a handover should be digitally signed off.
- Emergency readiness: Do your colleagues know what they need to do in the case of an emergency? Informing them of the due process if there’s an accident or emergency, is all part of a thorough PTRA.
- Control Measures: Including control measures that are appropriate for your industry, will help mitigate risks and promote safety. Some common examples of these are:
- Engineering – for example installing machine guards to prevent contact with moving parts.
- Administrative – examples including setting out clear work protocols for both executing tasks and job-rotation schedules
- Personal Protective Equipment (PPE) – controlling clothing and equipment is up-to-standard and an inventory of everything needed to get the job done.
- Environmental – ensuring temperature, lighting, cleanliness, humidity is all up to standard.
- Staff training – ensuring all staff that are undertaking hazardous tasks have the appropriate training and experience.
- Risk Analysis: A detailed risk analysis including potential hazards, defects, exposure to human mistakes and other potential on-site.
- Staff training & Internal Comms: Clearly communicate safety procedures, ensure staff managing the task are correctly trained, informed and with the right experience.
- Monitor and Review: Regularly assess control measures’ effectiveness, encouraging ongoing feedback to identify emerging risks and improve PTRP procedures.
- Document and Record Keeping: Maintain thorough documentation of PTRP assessments, hazard assessments, and corrective actions for future reference and regulatory compliance.
The 3 common mistakes of a Pre-Task Risk Assessment and how to avoid them
Once you have your PTRA template in place, remember that there are some common pitfalls that inevitably crop up, especially in an environment with varying and often unpredictable work-conditions. We have listed 3 common mistakes when conducting a PTRA so you can hit the ground running.
- Excluding colleagues from the PTRA process: One common mistake is neglecting to include colleagues and especially frontline workers from the risk assessment process. Underestimating the need to inform, educate and encourage a two-way conversation with colleagues about what works and what doesn’t is necessary to avoid incomplete assessments. Engagement fosters ownership and accountability.
- Failing to monitor and update assessments: Once a PTRA is created, schedule reviews of the template at fixed intervals, and have a control mechanism in place which will let the system flag when changes have taken place, such as personnel or equipment turnover. Having a designated person responsible who stays informed of regulatory updates is always recommended.
- Underestimating the dynamic nature of tasks: Like how one shouldn’t underestimate the shifting nature of work with personnel changes and so on, the very tasks that need executing can also be dynamic and vary in complexity and scope. Don’t ignore these variations in favour of a one-size fits all PTRA template. Customizing your routines will uncover potential risks.
CheckProof’s approach to enhanced safety with PTRA templates and HSE compliance
Integrating a tool like CheckProof can help enhance on-site safety and with quick and easy set-ups as well as continual updates your routines will stay dynamic and your site HSE compliant.
This is how it works:
- Customizable Templates: Set up all the necessary routines in a digital format that’s both simple to navigate and custom-built.
- Instant Messaging: Let members of your team communicate in real-time on within the system to allow them to share updates and stay on the same page.
- Centralized Document Management: All your documentation is readily accessible when needed and all on one system.
- Automated Reminders: Receive automated reminders of upcoming PTRA checks, activities and deadlines.
- Actionable Insights: With powerful reporting tools on your fingertips, you can get insight into recurring hazards and areas of improvement with a data-driven approach. The ability to add photos and videos provides a great record for reference as well as giving an insight into the site conditions at the time of the assessment.
Pre-task risk assessment is a key building block in a robust safety management system, but its success will depend on how vested your team is in its implementation and how adaptable the system is that you conduct your PTRA in. Failure to plan for risk is simply taking too high a risk.
So next time, you find yourself asking, ‘what the PTRA?’ – Give us a call.
Want to know what CheckProof can do for you?
CheckProof's easy-to-use app makes it easier to do the right thing at the right time. Discover how you can run world-class maintenance that is both cost-effective and sustainable.




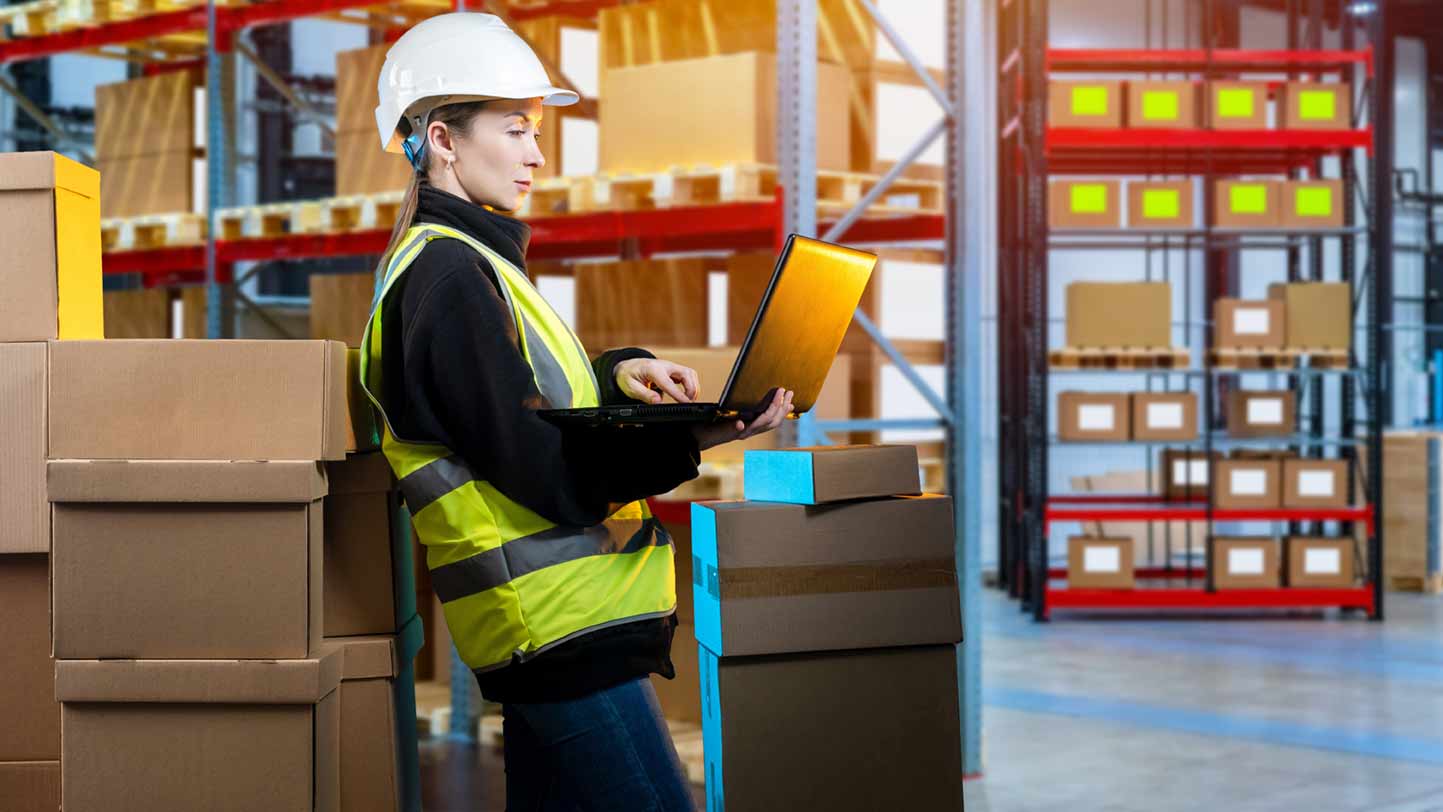

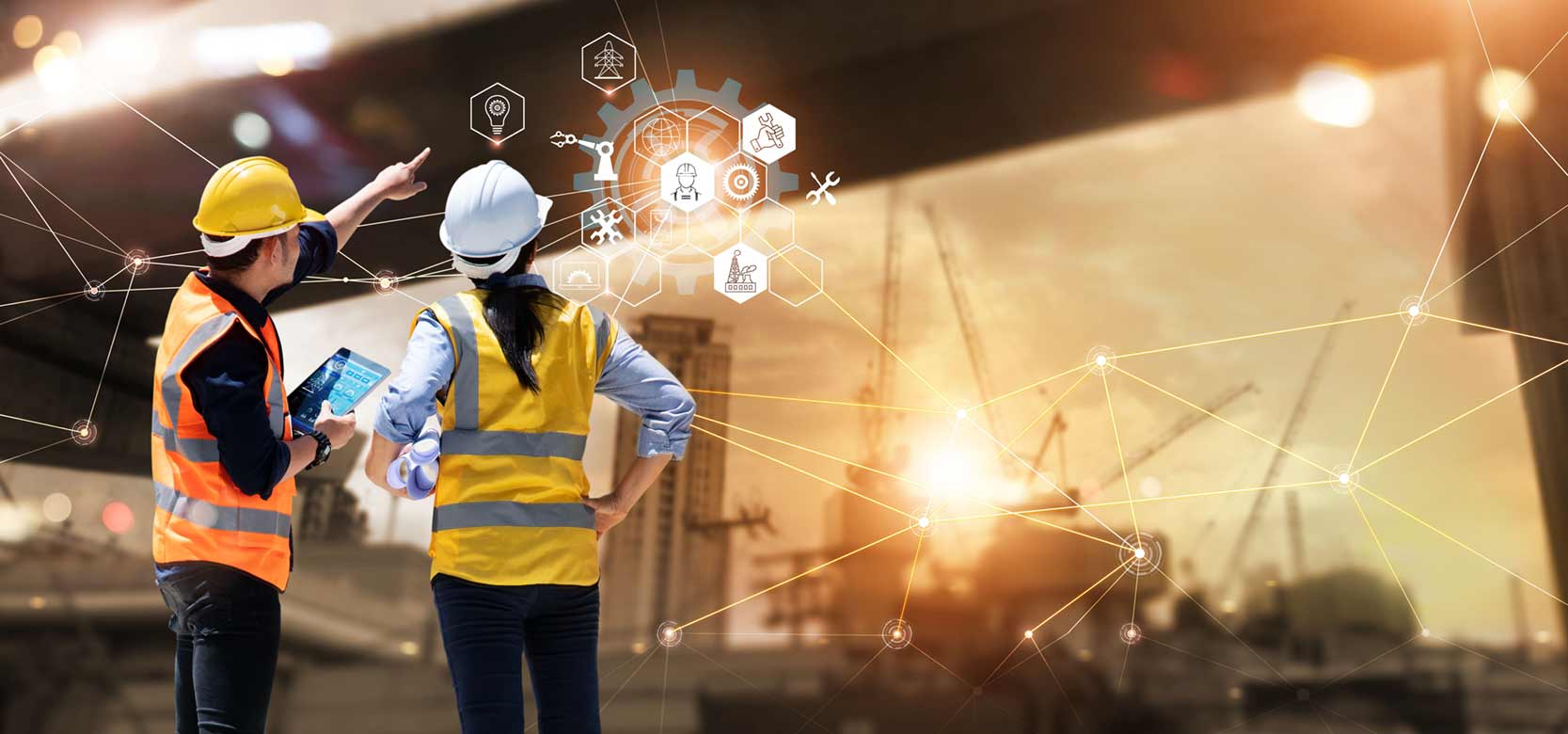


