There’s a lot of truth in the expression “what gets measured gets done”. Unless you start tracking the causes of unplanned downtime or breakdowns in your facilities, you won’t know what measures to take to improve availability in the future. Therefore, documentation and traceability are key to reduce downtime. But how do you prioritise these matters in a busy workday? These four tips will help you succeed.
1. Build a continuous improvement culture
Making sure everyone knows what they’re supposed to do is one thing; getting that bevaviour to really stick in the group on a day-to-day basis is a different matter. To succeed requires clear leadership and division of responsibilities. The employees need to understand the purpose – and see the results of – following the established routines and documenting every defect and deviation. Otherwise, lack of motivation (and human error) will lead to negligence, low priority, and important data not being recorded. Again, continuous follow-ups are crucial. They will show the long-term results of performing tasks that might be difficult to see the immediate impact of and allow plant managers to detect if anything has been neglected. Doing the right thing should be easy and rewarding; not doing it needs to have consequences – before it causes another unplanned stoppage.
Find out more in the article How to establish a continuous improvement culture for your facility.
2. Simplify, and digitize frontline reporting
The bigger the facility, the more there is to control and document, which becomes overwhelming if done on paper. More and more companies use digital systems for documenting and following up on stoppages and downtime (caused by acute corrective maintenance or other disruptions), as well as detailed checklists and routines for preventative maintenance tasks. This enables extensive documentation with categorisation, photos, and comments showing the full historic records – without requiring vast resources; neither in time nor storage space. By connecting the control systems of your machines, vehicles, or facilities, you can make sure different routines are activated automatically after a specified production time, mileage, or number of produced units. This makes your maintenance work more accurate than if a routine is carried out at a fixed time interval, regardless of the actual production during the time span.
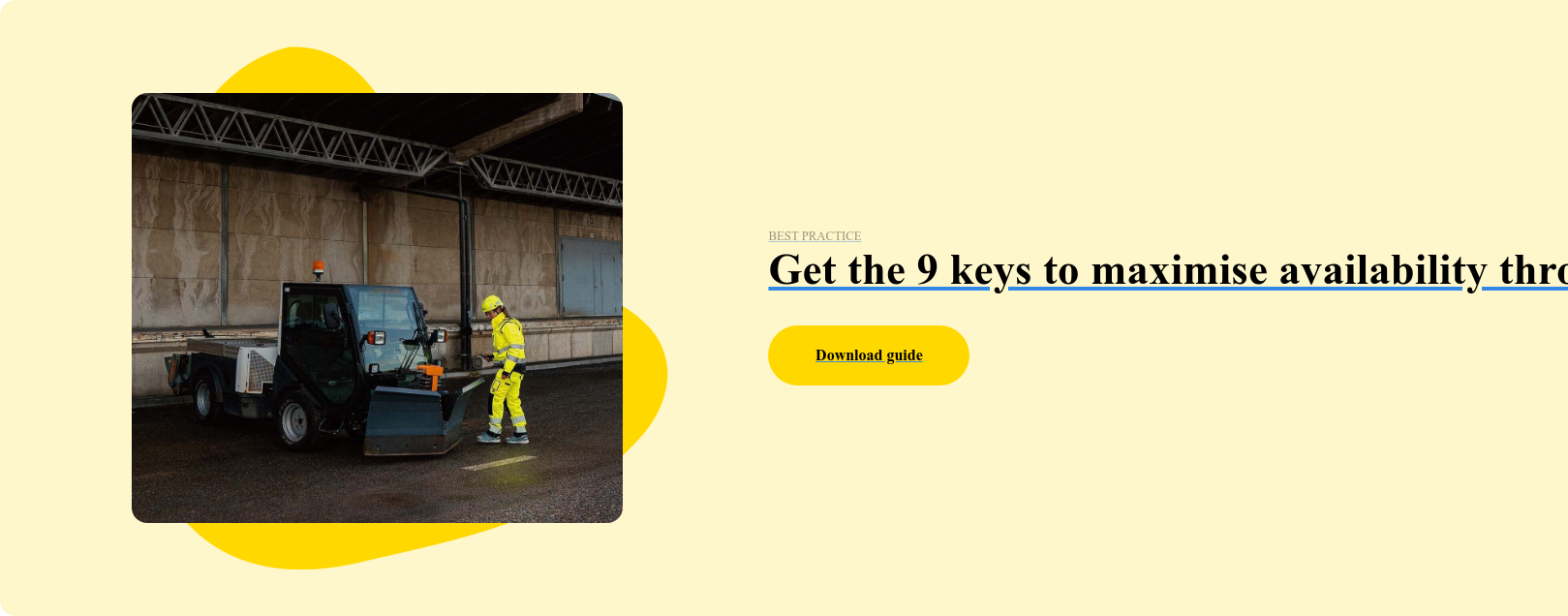
3. Keep a downtime log
Keep a downtime log that includes all forms of standstills, disruptions, and acute corrective maintenance that cause downtime. Make sure the documentation is as detailed as possible with photos and comments to clearly show what led up to the stoppage, which part of the facility caused it, as well as how long the downtime lasted, and what measures were taken to solve the problem.
By continuously collecting this data, you can start mapping out which types of issues are causing the most disruptions to planned production. That way, you’ll have the facts in place to make well-informed decisions that will reduce unplanned downtime in the future. Examples of measures could be improving routines and processes or calculating the ROI of larger investments needed to eliminate the root cause of recurring stoppages. The documentation in the log also minimises the risk of important information being lost if someone in the team should fall ill or leave the company.
4. Do continuous follow-ups
Documentation is an important first step, but without a proper follow-up, it won’t provide the desired results. Don’t let your documentation collect dust on a shelf somewhere. Identify stoppages where you see a pattern as well as the biggest potential for improvement. Analyse the root causes and set up an action plan to design them out or create additional routines to minimise future breakdowns. Include continuous follow-ups as a regular part of the agenda on weekly or monthly staff meetings. That way, you’ll show staff that these matters are prioritised by the company. It also means important lessons can be learned and shared directly with the entire team.
Want to know what CheckProof can do for you?
CheckProof's easy-to-use app makes it easier to do the right thing at the right time. Discover how you can run world-class maintenance that is both cost-effective and sustainable.

Revolutionizing Compliance: Banner Contracts on managing ISO audits with CheckProof

Implementation of Digital Systems: Rolling Out CheckProof Across Teams

From Fuel Savings to Production Gains: Cemex Germany’s Wins with CheckProof

A Recap of the CheckProof Industry Event & 10th Anniversary Celebration
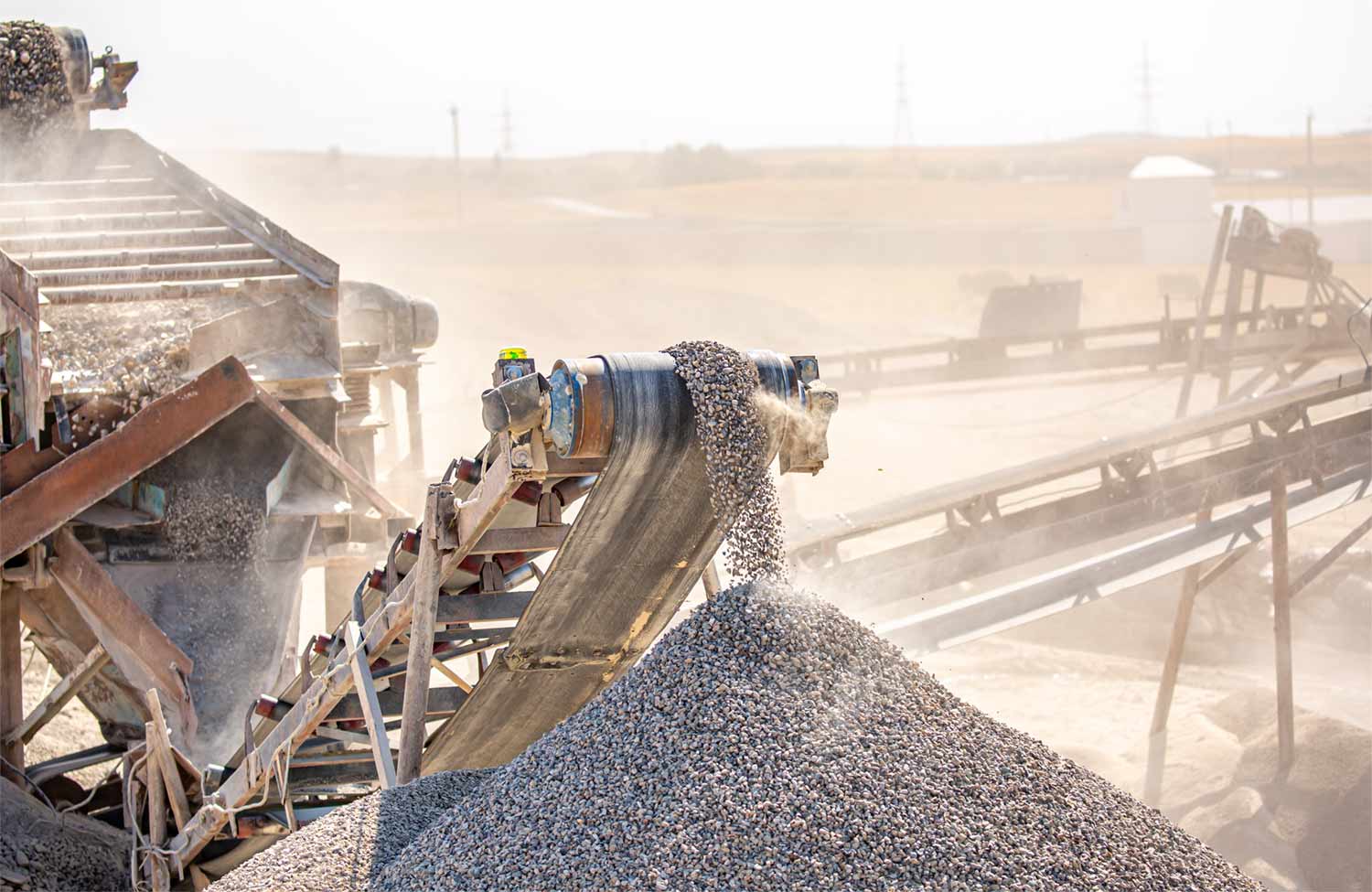
Trend Report: Key moments in the Construction Materials industry (2014–2024)

Meet Marcus Edlund, CheckProof’s First Employee and Tech Trailblazer

10 Key Technology Advancements in the Construction Materials Industries

SBMI’s Climate Roadmap for a Fossil-Free Aggregate Industry by 2045

HSEQ trends in the Construction Materials and Heavy Industry
