Join us at AGG1, St Louis, MO - America's Center Convention Complex: 25-27 March
There is an increased awareness and acceleration within the heavy industries on how ‘Routine Maintenance’ workflows should replace traditional reactive maintenance methods for the upkeep of equipment and the wellbeing of personnel. Routine Maintenance when done well can form the backbone of any well-functioning system, whether it’s a piece of machinery, a vehicle, or even a building.
In this article, we’ll dive into why keeping a proactive mindset and integrating routine maintenance into your workflow is key to enhancing safety and increasing asset longevity. We will cover:
- What is Routine Maintenance?
- Real Examples of Routine Maintenance
- Challenges with Traditional Routine Maintenance
- 7 different types of common Routine Maintenance practices
- Create a Routine Maintenance workflow process
- Digitizing Routine Maintenance
What is Routine Maintenance?
Routine maintenance often refers to the planned (and scheduled at timed intervals) upkeep of equipment, machinery, systems, buildings, or infrastructure to ensure they remain in good working condition and operate efficiently. The purpose of routine maintenance is to prevent breakdowns, extend the lifespan of assets, reduce the risk of accidents or failures, and maintain optimal performance.
Real Examples of Routine Maintenance
Examples of routine maintenance span various industries and applications, including:
- HVAC Systems: Regular filter replacement, coil cleaning, and system checks to ensure optimal performance and energy efficiency.
- Fleet Vehicles: Scheduled oil changes, tire rotations, and brake inspections to prevent breakdowns and ensure driver safety.
- Manufacturing Equipment: Lubrication, calibration, and alignment checks to prevent wear and tear, maintain accuracy, and minimize downtime.
- Commercial Buildings: Routine inspections of electrical systems, plumbing, and structural integrity to address potential hazards and ensure occupant safety.
Challenges with Traditional Routine Maintenance
Traditional and out-of-date maintenance methods can often face several challenges, such as:
- Reactive Approach: Plants are often hit with unexpected and highly undesired downtime due to a lack of accounting for routine maintenance planning. The result can often be that equipment breaks down before action is taken. This leads to costly repairs, downtime – and in the worst case, compromised safety for staff.
- Inefficient Scheduling: Traditional methods may rely on fixed schedules rather than the actual condition of your assets. So, if a defect or deviation has gone unnoticed, it may not be until the next scheduled check that the problem is discovered – causing further unnecessary fixes, lengthier involvement from all involved to correct the issue and an overall waste of resources.
- Limited Visibility: Lack of real-time data and insights makes it difficult to anticipate maintenance needs and prioritize tasks effectively and to the appropriate teams.
- Paper-based Documentation & Manuals: Paper-based documentation and lengthy manuals that can only be found in binders in an office cupboard are a recipe for inefficient maintenance workflows. In extension this will lead to errors, missed checks, leading, lack of traceability, and a challenge to keep plants and assets compliant.
- Resource Allocation: This is true for both Reactive Maintenance as well as Planned Routine Maintenance. There is certainly an upfront investment in terms of staff time and cost when you put scheduled routines in place. This can create resistance to implementation. However, anyone who has experienced lengthier machinery downtime, or accidents at their plant, likely recognizes this will incur a far greater cost in the long run, whilst also causing unplanned staff scheduling issues.
7 different types of common Routine Maintenance practices
- Failure Finding Maintenance: As the name suggests, this is a proactive approach to identify potential failures before they even occur through regular inspections and tests, minimizing unexpected downtime.
- Condition-Based Maintenance: Real-time monitoring of equipment condition using sensors and data analysis, enabling informed decisions and optimized maintenance schedules.
- Predictive Maintenance: Anticipating equipment failures through advanced analytics and predictive modeling, maximizing asset reliability while minimizing downtime and costs.
- Corrective Maintenance: Identifying the beginning of an issue, but applying corrective action before it becomes a major issue.
- Emergency Maintenance: Urgent repairs to address critical failures or safety hazards, requiring quick mobilization of resources and personnel. This is the least desirable of all maintenance outcomes.
- Risk-based Maintenance: Prioritizing maintenance activities based on asset criticality and potential failure consequences, optimizing resource allocation and decision-making.
- Routine Maintenance Workflow: Systematic planning, scheduling, execution, and documentation of routine maintenance activities, ensuring consistency, compliance, and efficiency in maintenance operations.
Create a Routine Maintenance Workflow Process
Effective routine maintenance involves a systematic workflow process, but before you start creating one from scratch, consider downloading this guide, which holds insider tips on how leaders in the heavy industry go about creating incredibly efficient processes to run their plants. A Routine Maintenance process will often contain the following elements:
- Inspection: Conduct thorough inspections to assess equipment condition, identify potential issues, earmarking the assets that need routine maintenance.
- Planning: Digitize and download manuals for the chosen assets to understand scheduling needs and the resources you must allocate to keep the workflow running smoothly.
- Scheduling: This can be trickier than you think. As wrote scheduling or overscheduling can lead to carelessness and diminishing returns on the assets. Involving operators in this part is crucial to get a thorough understanding of how often your assets need to be checked.
- Maintenance Execution: Performing necessary maintenance activities, repairs, and replacements according to the schedule that has been implemented.
- Documentation: Recording maintenance data, including work performed, parts replaced, and any observations.
- Analysis: Analyzing maintenance data to identify trends, optimize schedules, and improve processes.
- Continuous Improvement: Implementing feedback loops and making adjustments to enhance efficiency and effectiveness.
- Use CheckProof’s maintenance calculator to calculate cost savings as a direct result of maintenance scheduling.
Digitizing Routine Maintenance with CheckProof
Digitizing routine maintenance practices with one system for everyone across the company has the power to achieve remarkable productivity gains and numerous practical benefits such as:
- Real-time Visibility: Access to up-to-date equipment data and insights from anywhere, anytime.
- Automated Alerts: Proactive notifications for maintenance tasks, upcoming inspections, and potential issues.
- Streamlined Workflows: Simplified scheduling, task assignment, and documentation processes, reducing administrative burden.
- Data-driven Decision Making: Analysis of historical data and predictive analytics to optimize maintenance strategies and resource allocation.
- Enhanced Compliance: Digital records and audit trails for regulatory compliance and accountability.
Routine maintenance is not just a necessity, but a clever strategy for organizations seeking to meet productivity, sustainability, and cost-saving targets. Embracing a digital platform, like CheckProof to create maintenance workflows, enables businesses to stay ahead of the curve, minimize risks and downtime, and unlock new opportunities for growth and innovation.
Want to know what CheckProof can do for you?
CheckProof's easy-to-use app makes it easier to do the right thing at the right time. Discover how you can run world-class maintenance that is both cost-effective and sustainable.

Maximize Efficiency with an OEE Monitoring System
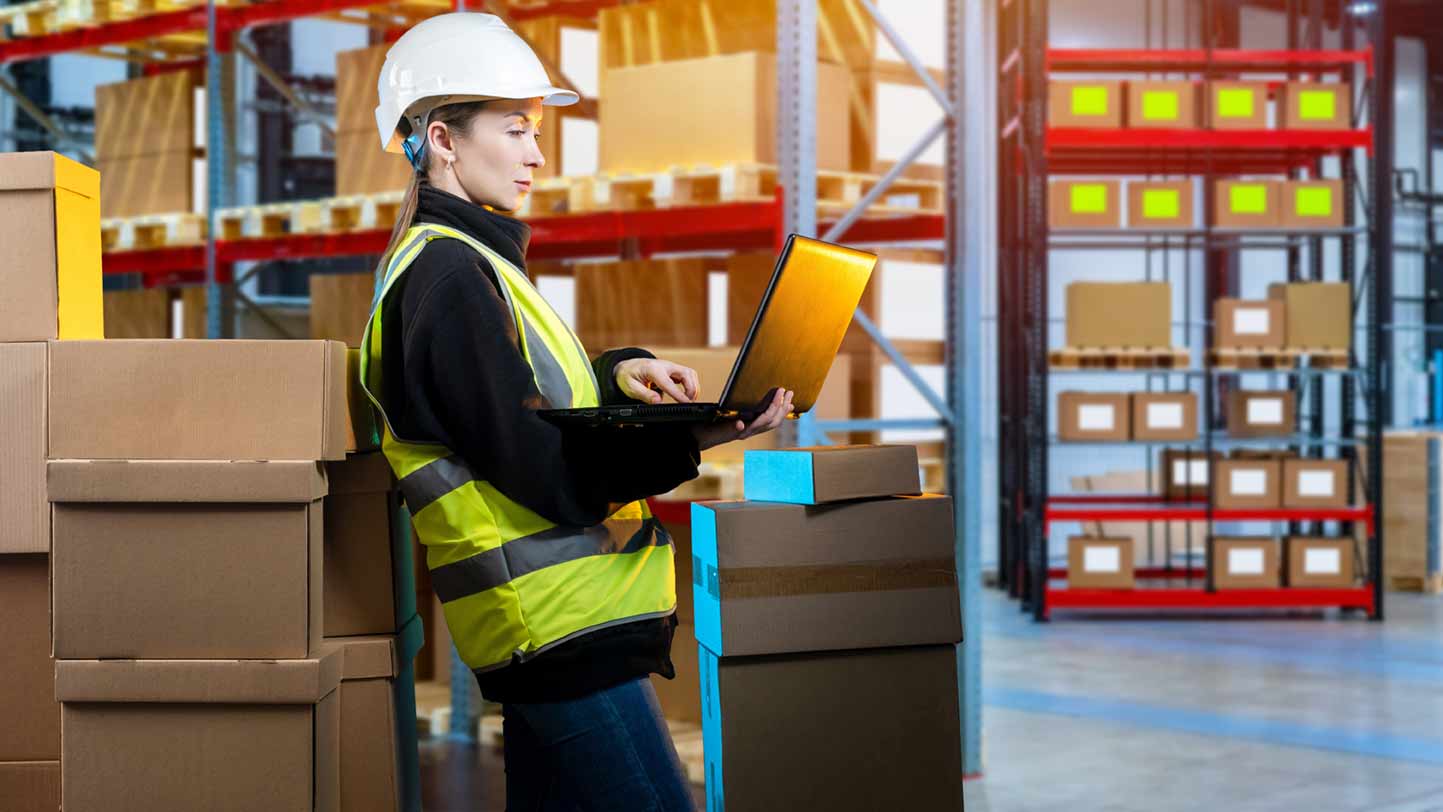
Plant Asset Management Software:Maximizing Equipment Uptime

Machine Downtime Tracking: The key to smarter, more efficient operations
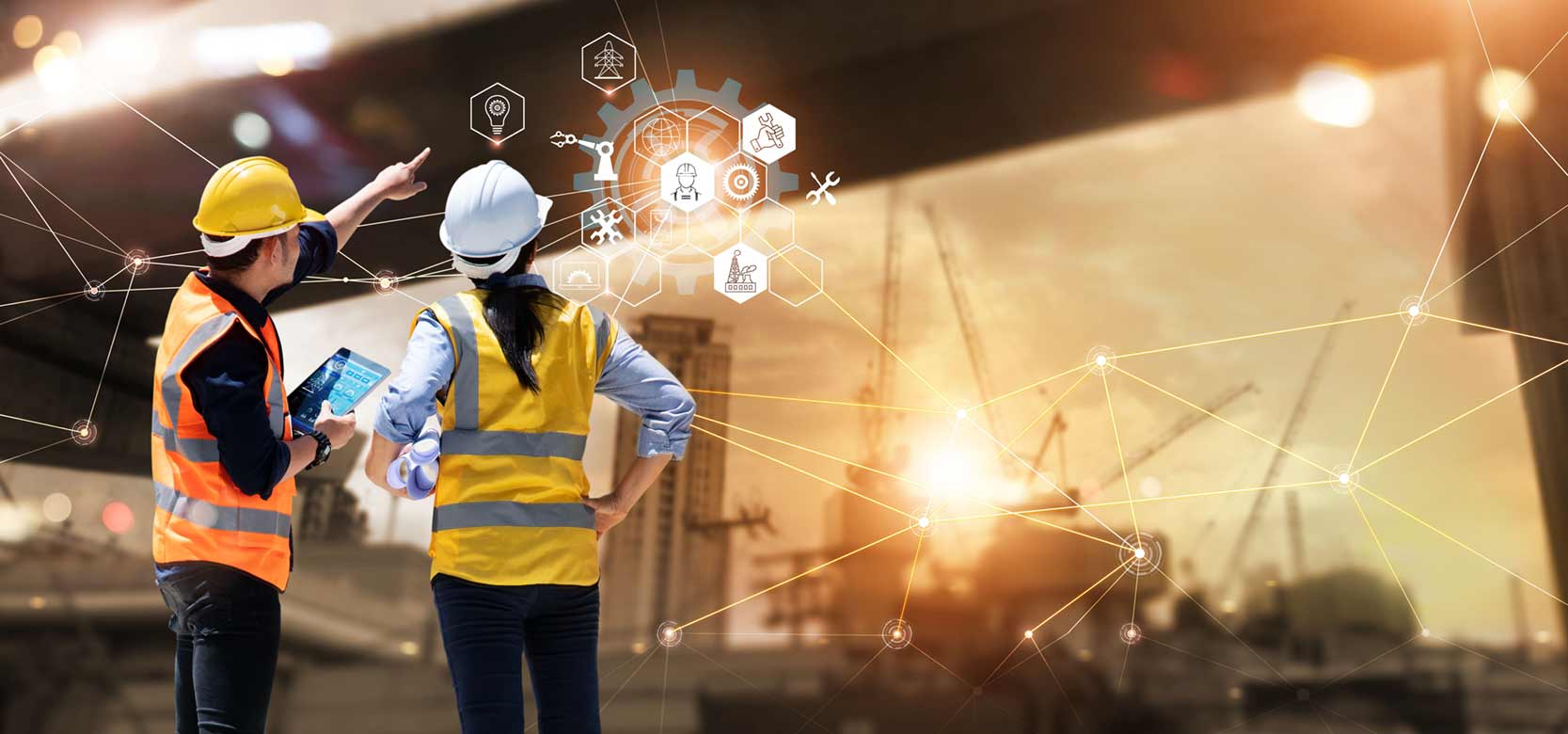
CMMS Software: What it is and why it’s key to First-Class Maintenance Operations

Revolutionizing Compliance: Banner Contracts on managing ISO audits with CheckProof

Implementation of Digital Systems: Rolling Out CheckProof Across Teams

Von Kraftstoffeinsparungen bis hin zu Produktionssteigerungen: Wie Cemex Deutschland erfolgreich CheckProof implementiert hat

A Recap of the CheckProof Industry Event & 10th Anniversary Celebration
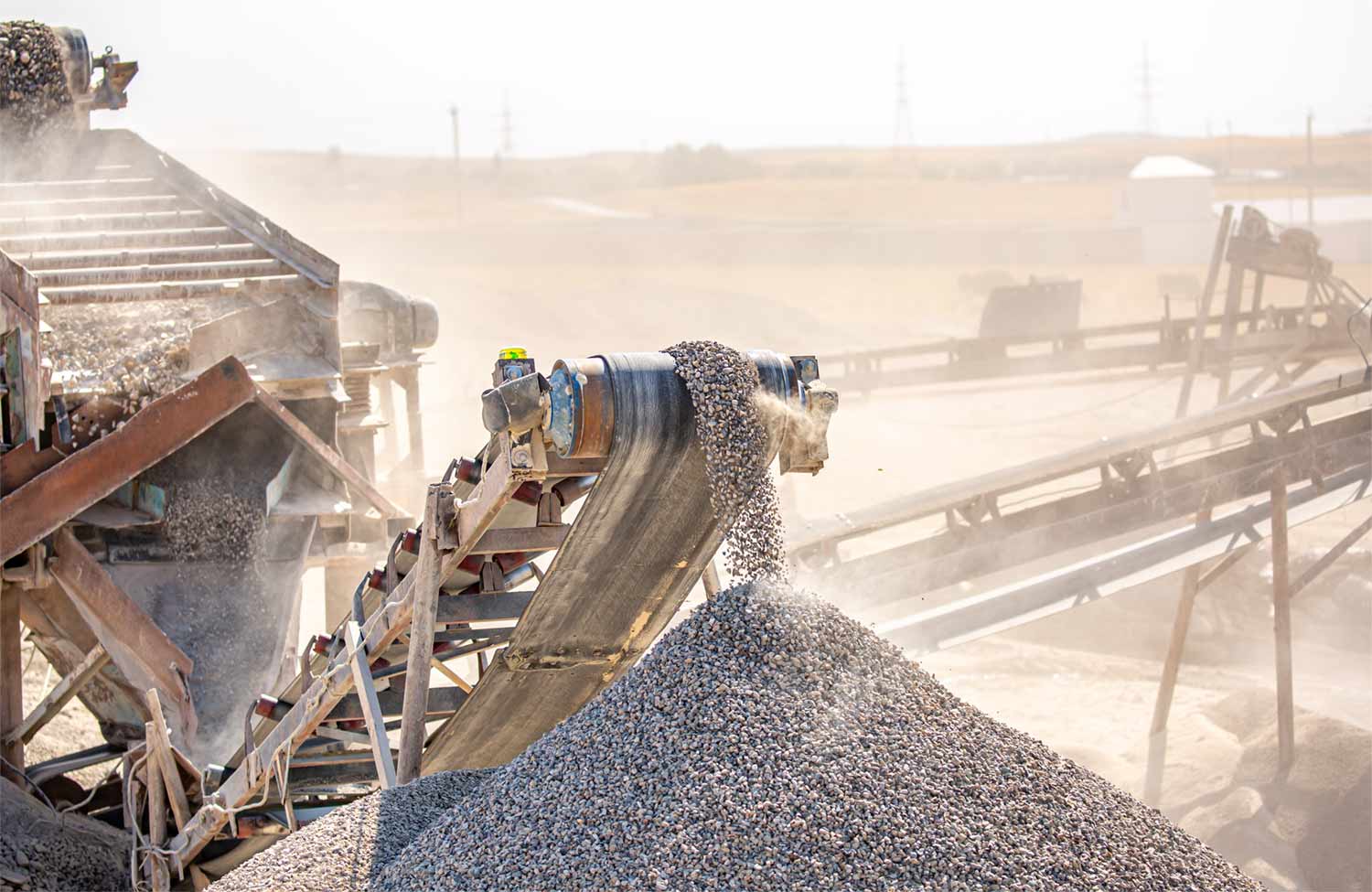
Trend Report: Key moments in the Construction Materials industry (2014–2024)
