Keeping assets in top shape and extending their lifespan is a key priority for maintenance managers—right after preventing equipment failure and downtime! In the construction materials industry, where heavy equipment and infrastructure are essential, keeping assets in peak condition is crucial for maintaining efficiency and reliability. Plant asset management software helps businesses track, maintain, and optimize equipment performance, reducing downtime and improving efficiency. With the right asset inspection management software and condition report app, maintenance teams can use condition-based data instead of calendar-based maintenance schedules to perform inspections, ensuring no critical task is missed.
This article covers:
- Plant Asset Management Software: What is it?
- 8 Key Benefits of Plant Asset Management Software
- Asset Inspection & Plant Asset Management Software: Key Features
- Condition Report App combined with Asset Management Software
- Choosing the right Asset Management Solution
- Is CheckProof’s Platform the Right Fit for Asset Management?
Plant Asset Management Software: What is it?
Plant asset management software is designed to optimize asset health, performance, and inventory management. By gathering data from plants, sites, and mixed fleets, it centralizes critical information into a single platform for better visibility and control. An effective system can help improve overall equipment efficiency (OEE) by identifying recurring breakdown patterns and by capturing data from sensors attached to machines triggering maintenance alerts before they become critical. It essentially applies a predictive maintenance method to optimize equipment performance. It has similarities to a CMMS (Computerized Maintenance Management System) software but is often regarded as more complex in scope, as the software relies on streaming telematics data and integrations to monitor asset health. It is therefore also sometimes referred to as Enterprise Asset Management.
As Asset Management Software is designed to optimize the performance, reliability, and lifespan of critical equipment, its efficiency depends on how well it can integrate telematics and real-time data.
8 Key benefits of Plant Asset Management Software
Cement and asphalt plants, quarries, and heavy industry, in general, depend on well-maintained equipment. When machinery fails, production suffers immediately, leading to costly delays and a knock-on effect on stocks and client orders.
A major advantage of asset management software is that it makes the cost of equipment failure instantly visible. Integrating it with analytics tools like Power BI and Tableau transforms reporting into a strategic advantage. By consolidating asset performance data, businesses gain deeper financial insights—tracking maintenance costs, optimizing resource allocation, and identifying inefficiencies. Real-time analytics help forecast expenses, reduce unplanned downtime, and extend equipment lifespan, ultimately driving cost savings. With data-driven reporting, companies can make informed decisions that improve budgeting, boost ROI, and enhance overall operational efficiency.
- Cost Savings – Reduce unexpected repair costs and optimize resource allocation.
- Minimized Downtime – Proactive maintenance planning prevents costly breakdowns.
- Extended Asset Lifespan – Routine servicing keeps equipment in peak condition.
- Improved Safety – Prevent hazards with timely maintenance and inspections.
- Meeting Compliance – Ensure accurate audits and meeting regulated safety standards.
- Data-Driven Decisions – Gain deeper insights into asset performance and financial trends.
- Optimized Uptime – Keep equipment running at peak efficiency for maximum productivity.
- Sustainability Gains – Extend equipment lifespan and reduce waste by lowering emissions and minimizing resource consumption.
Asset Inspection & Plant Asset Management Software: Key Features
The terms Asset Inspection Software and Plant Asset Management Software are sometimes used interchangeably, but they can have different features depending on the system you choose. Since effective maintenance starts with thorough inspections, a software solution focused on inspections should enable teams to log, track, and monitor asset conditions in real-time. A digital solution eliminates the need for paper-based records (read paper trails and countless binders), reducing errors and ensuring that critical maintenance tasks aren’t overlooked. When selecting a system, key features to look for include:
- Customizable Checklists – Build interactive checklists with predefined maintenance schedules, track if routines are followed and tasks checked off.
- Telematics Integration – Stream machine data to automate maintenance triggers based on usage.
- Real-Time Notifications – Get instant alerts on deviations, issues, and maintenance needs.
- Seamless Communication – Enable direct responses and issue resolution from the app.
- Visual Documentation – Upload photos, videos, and annotations to provide clear context for deviations.
- All-in-one platform – Manage all asset and telematics data in one platform without switching between systems.
- Offline Functionality – Perform inspections and log data without a network; everything syncs once reconnected.
- Task Assignment – Assign checks to teams or individuals to streamline responsibility and efficiency.
- Deviation Reporting – Create deviations directly from checklists for faster issue resolution.
By integrating asset inspection management software, companies improve operational efficiency and ensure compliance with safety standards.
Condition Report App combined with Asset Management Software
A condition report app enables teams to document asset conditions in real-time with a mobile app. Instead of relying on handwritten notes or spreadsheets, a digital tool ensures that every inspection is recorded accurately and accessible when needed.
For example, with CheckProof’s app, frontline teams can report deviations and faults quickly and easily from their mobile device this information is then combined with the asset data already available to give a comprehensive overview of the assets.
Key features of a condition report app should include:
- Real-Time Data Entry – Reduce paperwork and speed up reporting.
- Cloud Storage – Access to reports and checklists anytime, anywhere.
- Automated Alerts – Get notified when inspections reveal issues.
- Seamless Integration – Connect with other systems for smooth data sharing.
Choosing the Right Asset Management Solution
When selecting plant asset management software, businesses should consider:
- Scalability – Can it grow with your operations?
- Ease of Use – Is it user-friendly for frontline teams?
- Integration – Does it sync with existing ERP or CMMS systems?
- Mobile Accessibility – Can it be used on any device?
Is CheckProof’s Platform the Right Fit for Asset Management?
A platform like CheckProof, essentially has key elements of a CMMS and Asset Management Software rolled into one. The centralized platform is designed for monitoring and maintenance as well as connecting with telematics systems across mixed fleets, capturing vital insights like:
- fuel consumption
- location
- idle time
- error codes
- CO₂ emissions
- (regardless of equipment brand)
What also sets CheckProof’s platform apart is that it merges machine data with frontline reports (condition reporting app), CheckProof’s Plant Asset Management Software gives businesses complete visibility into asset health. It enables proactive maintenance, trend monitoring, and compliance tracking—all within a single platform. Additionally, integrations with OEMs and third-party providers for vibration sensors, temperature monitoring, and belt-weigher software help automate maintenance workflows. This ensures that plants operate at peak efficiency, turning raw data into actionable insights for smarter, more connected operations.
Furthermore, as CheckProof’s platform integrates with ERP systems through an API (Application Programming Interface) it enables real-time data exchange. By merging asset inspection data with ERP systems, businesses can reduce costs, and drive efficiency.
Investing in the right asset management software for your business will drive the data-driven insights necessary to extend equipment lifespan, minimize downtime, and improve overall operational performance, helping your operations maintain its competitive edge.
Want to know what CheckProof can do for you?
CheckProof's easy-to-use app makes it easier to do the right thing at the right time. Discover how you can run world-class maintenance that is both cost-effective and sustainable.




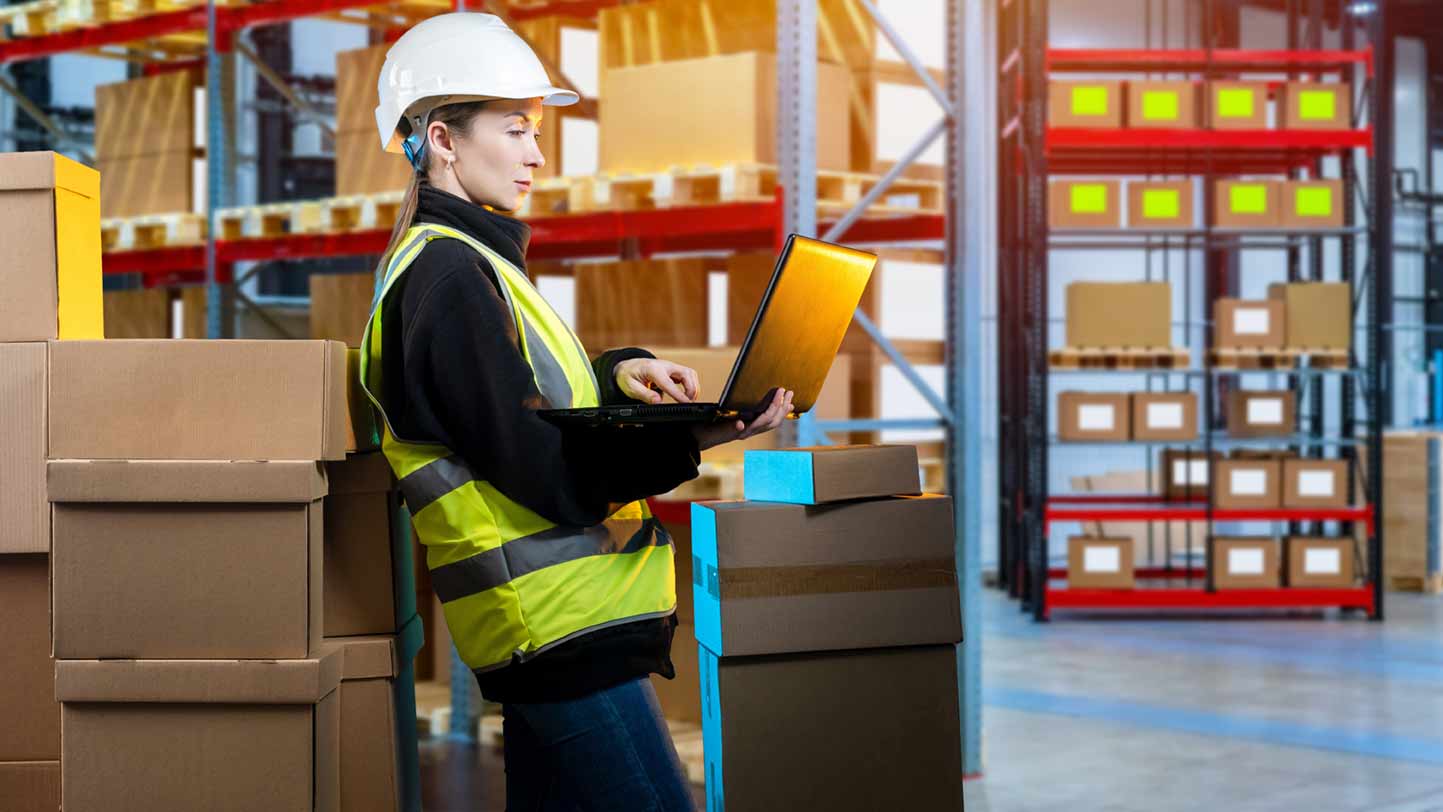

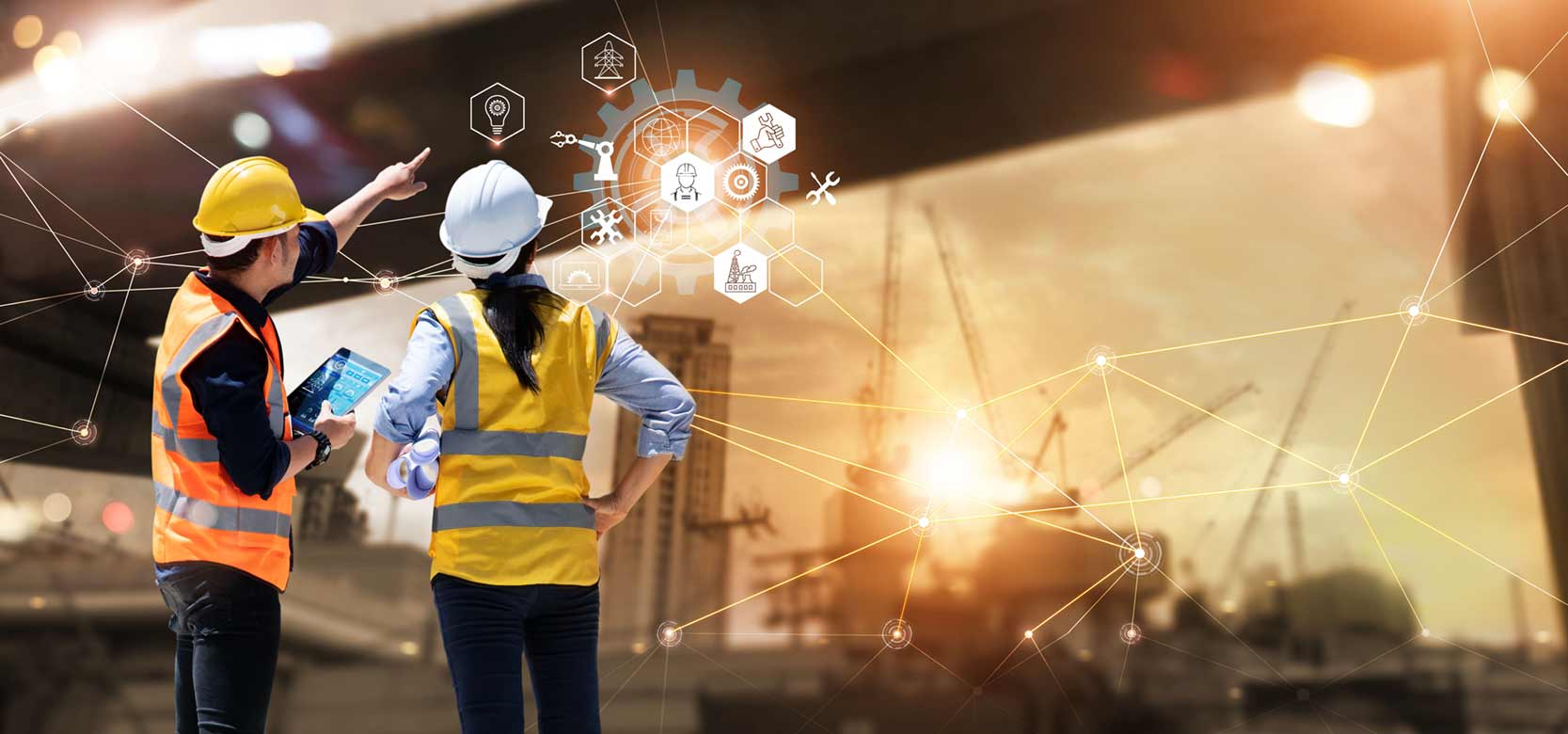


